7. Филиалы предприятия
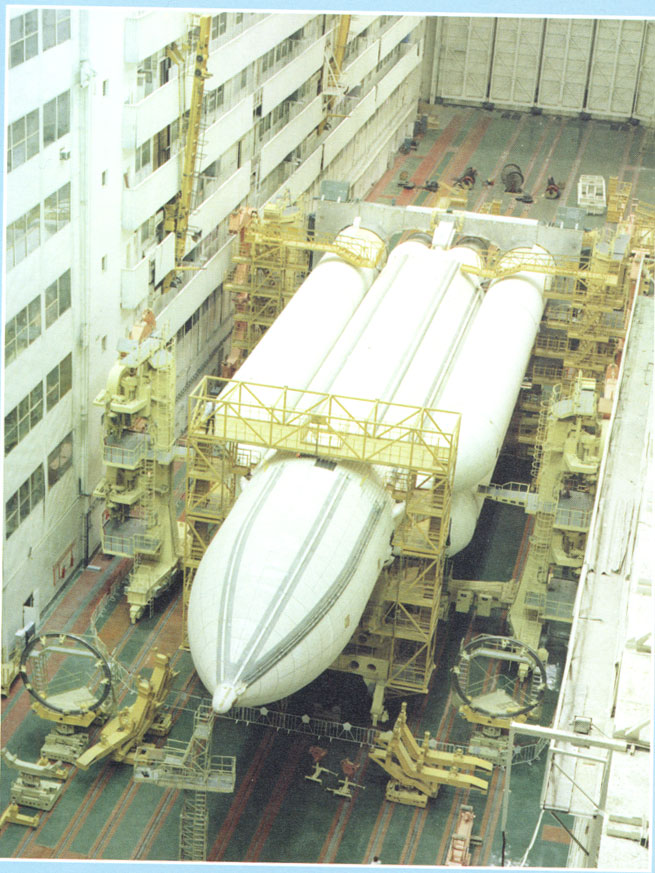 |
|
Волжский филиал
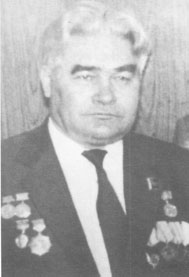
Б.Г. Пензин |
В 1959 году для сопровождения изготовления ракеты-носителя Р-7 (11А511) в г. Куйбышеве при заводе "Прогресс" (А.Т. Абрамов) был организован филиал ОКБ-1. Руководителем Куйбышевского филиала (КФ) назначили Д.И. Козлова, бывшего ведущего конструктора ракеты Р-7. Филиалу передали также тематику, связанную с созданием космических средств контроля за особо важными стратегическими объектами и развитием кризисных ситуаций в различных частях Земного шара. Первым космическим аппаратом для решения этих задач стал КА "Зенит", разработанный в ОКБ-1. Направление создания космических средств наблюдения получило свое дальнейшее развитие и стало основным видом деятельности Куйбышевского филиала ЦКБЭМ, а затем Центрального специализированного конструкторского бюро (ЦСКБ).
Работы же по теме "Энергия — Буран" были встречены руководством КФ ЦКБЭМ без энтузиазма, как тема, мешающая разработке космических аппаратов и сопровождению производства Р-7 на заводе "Прогресс".
И тогда принимается решение об организации нового филиала, теперь уже НПО "Энергия". Приказом министра общего машиностроения С,А, Афанасьева 30 июля 1974 года создается Волжский филиал (ВФ) НПО "Энергия". Руководство филиалом было поручено Б.Г. Пензину. Деятельность филиала начиналась в труднейших условиях, На арендованных у ЦСКБ площадях малочисленный коллектив сразу приступил к выпуску конструкторской документации на разработку центрального блока (блок Ц) ракеты-носителя "Энергия" и стартово-стыковочного блока (блок Я).
При подготовке к работам по изделию с новым для нашей ракетной техники экологически чистым топливом — водородом — были разработаны программы освоения нового криогенно-упрочняемого сплава 1201. Начались разработки документации на емкости РН "Энергия" в вафельном варианте, проводились анализ и выбор заготовок для создания обечаек крупногабаритных емкостей. Начальник и главный конструктор филиала Б.Г. Пензин, его заместитель И.П. Рябихин, начальники отделов П.И. Кирсанов, В.П. Прокофьев, Н.Н. Гниломедов, А.В. Андреев, Б.В. Тюлин, В.С. Филиппович, Н.С. Головашев, уже имевшие большой опыт в разработке документации и изготовлении изделий на производстве и значительную заводскую закалку, смогли организовать свои коллективы, быстро преодолеть этап становления.
В 1976 году были закончены разработки разделов в ЭП на блоки Ц и Я ракеты-носителя "Энергия", выданы исходные данные на проектирование технологического оборудования заводу "Прогресс" и отраслевому институту. Большую работу по отработке методов сварки емкостей и созданию оборудования для нее проводил коллектив технологов предприятия под руководством Д.Ф. Яковлева с Институтом сварки им. E.O. Патона Академии наук УССР (Б.Е. Патон).
В 1975 году была окончательно принята компоновочная схема ракеты-носителя "Энергия" в двухбаковом варианте центрального блока, и в этом же году начато изготовление панелей обечайки бака горючего блока Ц. В тесном сотрудничестве с заводскими специалистами коллектив ВФ НПО "Энергия" взял на себя ответственность за начало изготовления материальной части, пока еще не выпустили всю документацию и не провели основные экспериментальные работы. Основная заслуга в этом принадлежит коллективу прочнистов, одному из сильнейших в ракетно-космической отрасли, возглавляемому А.В. Андреевым. Коллективы службы прочности, применяя новейшие методики расчета, широко используя ЭВМ, обеспечили оптимальные весовые характеристики конструкции с минимальными запасами по прочности.
Требования прочности определили необходимость создания уникальной испытательной базы на заводе "Прогресс" — базы статических и криогенно-статических испытаний, Она включала в себя стенд криогенно-статических испытаний, единственный в стране да и мире по своим возможностям. Этот стенд позволил проводить криогенно-статические испытания емкостей с заполнением жидким азотом с приложением к изделию внутреннего давления и системы сосредоточенных сил. Наружная поверхность камеры стенда теплоизолирована армированным пенополиуретаном. Камера высотой 40 м имеет внутренний диаметр 8,6 м, что позволило помещать в нее полноразмерный бак горючего РН "Энергия".
Кроме стенда КСИ база имеет стенд статических испытаний для проведения зачетных прочностных испытаний, в том числе испытаний до разрушения емкостей, что позволило экспериментально определить несущую способность и жесткостные характеристики полноразмерных баков РН. Стенд гидроиспытаний предназначается для проведения испытаний на прочность и герметичность отдельных обечаек и днищ баков, расходных и тоннельных трубопроводов емкостей больших диаметров. Создание стендов позволило избежать ошибок в проектировании и обеспечило успешную работу изделия. Коллектив комплекса 5 (Э.Н. Щербак) успешно справился с этой работой.
В 1979 году начались и успешно завершились работы по водно-автомобильной транспортировке экспериментальных емкостей и бака горючего в г. Жуковский Московской области. Проблема транспортировки грузов такого габарита на расстояние более 1000 км в условиях пересечения многочисленных промышленных зон была решена впервые коллективом конструкторов под руководством начальника комплекса А.Л. Маркина, руководителей отделов Б.П. Неудахина, Ю.Н. Порунова. В 1982 году приступили к изготовлению изделия 4М для проведения макетирования и холодных заправок. В этом же году на заводе "Прогресс" и других смежных предприятиях начали изготовление и отработку арматуры. Для обеспечения этого серьезнейшего участка работы с изделием на предприятии создается комплекс 3. Внимание к отработке арматуры было огромным: начальник главка министерства П.Н. Потехин, главный инженер завода "Прогресс" В.И. Ментюков неделями не выходили из цехов сборки арматуры. Конструкторы и руководители комплекса 3 А.А. Быстров, Ю. А. Овчаров, В.А. Александров, В.Д. Варивода обеспечили необходимое качество документации, ее изготовление и отработку. Арматура сработала в полете без замечаний.
Для обеспечения изготовления блоков Ц и Я, арматуры, трубопроводов, сильфонов приказом министра было привлечено более 20 смежных предприятий отрасли. Организационную работу по этому направлению взял на себя коллектив ведущих конструкторов под руководством Н.И. Харченко. Вопросы ведения производства по РН "Энергия" стали первоочередной задачей коллектива как на основной территории в г. Куйбышеве (сегодня г. Самара), так и в филиале завода — космодроме Байконур. 2 августа 1985 года изделие 4М было вывезено на стартовую позицию, начались работы по примерке и отработке изделия и стартовых сооружений. На космодроме работала большая группа конструкторов и испытателей, было создано специальное конструкторское бюро под руководством Г.Г. Романова, которое обеспечивало сборку и испытание изделий. Сто крупных экспериментальных установок для подтверждения конструкторских, проектных и прочностных решений было создано и испытано специалистами ВФ НПО "Энергия". В 1986 году началась подготовка к пуску изделия 6СЛ. Было принято решение пускать стендовую машину, доработав ее под летную. Начальник филиала Б. Г. Пензин, понимая важность социально-бытовых проблем, большое внимание уделял вопросам жилья для сотрудников предприятия и их отдыха. В том же 1986 году было начато строительство дома отдыха "Солнечный" на берегу Волги в одном из красивейших уголков Жигулей, напротив села Ширяево, где Репин писал "Бурлаков". Сегодня "Солнечный" — благоустроенный дом отдыха с асфальтированной дорогой, удобными коттеджами, столовой, оснащенный необходимым инвентарем и оборудованием для отдыха. Кроме сотрудников предприятия в нем отдыхают гости из Москвы, Киева, Риги, Одессы, Ленинграда и других городов.
В 1986 году ВФ НПО "Энергия" получил свое здание — корпус АББ-56 на территории завода "Прогресс" площадью 11 800 м . В этом же году начальником и главным конструктором предприятия был назначен С.А. Петренко (Б.Г. Пензин ушел на заслуженный отдых). Успешные пуски ракеты "Энергия" в мае 1987 и ноябре 1988 года были лучшей наградой коллективу Волжского филиала, который разделил успех со всеми участниками создания РН "Энергия". В этом успехе несомненна заслуга коллективов Ю.И. Зиканова, А.А. Маркина, А.А. Быстрова, А.В. Андреева, Э.Н. Щербака, Б.А. Труфанова, коллективов В.В. Огарева, В.Ф. Сергеева, В.П. Рябова, Н.И. Харченко и многих рядовых работников предприятия. Коллектив ВФ НПО "Энергия" приобрел громадный опыт работы с криогенными компонентами, в том числе и с жидким водородом в больших объемах. Такого опыта не имеет ни одно предприятие в нашей стране.
Начиная с 1989 года коллектив ВФ НПО "Энергия" включился в разработку РН "Энергия-М". Была выпущена вся конструкторская документация, однако прекращение финансирования приостановило дальнейшие работы. Начались поиски новых направлений работ, ВФ НПО "Энергия" включился в разработку РН "Ангара", а также создание ракет легкого класса для коммерческого использования.
С 1994 года, после приватизации, Волжский филиал НПО "Энергия" является дочерним предприятием РКК "Энергия" и
называется Волжским конструкторским бюро РКК "Энергия".
Приморский филиал

В.В. Елфимов |
Начиная с 1949 года ОКБ-456 (В.П. Глушко) совместно с Государственным институтом прикладной химии (ГИПХ, В.С. Шпак) проводились работы по изучению возможностей использования высокоэффективных компонентов топлив (фтор, моноокись фтора, пентаборан, аммиак, гидразин и др.) в ракетных системах и, в первую очередь, при отработке процессов, происходящих в жидкостных ракетных двигателях. Для практического освоения новых компонентов ракетных топлив на территории объекта ГИПХ (на 117 км Приморского шоссе в Ленинградской области) лабораторией ОКБ-456 в 1953-1957 гг. были построены первые четыре стенда и начаты работы по испытаниям модельных камер сгорания с целью выбора оптимального сочетания компонентов и создания базовых элементов конструкции будущих двигателей.
Постановлением от 20 марта 1958 года и Приказом ГКОТСМ СССР от 11 апреля 1958 года экспериментальная испытательная база ОКБ-456 преобразуется в филиал 1 ОКБ-456 с задачами отработки ракетных двигателей, использующих высокоэффективные криогенные и токсичные компоненты топлив. Первым начальником филиала 1 назначается Е.Н. Кузьмин.
При переименовании ОКБ-456 в 1965 году в ОКБ энергетического машиностроения (Постановление от 2 марта 1965 года) филиал 1 был переименован в Приморский филиал ОКБ энергетического машиностроения (ОКБ ЭМ). Приказом по Министерству общего машиностроения СССР от 22 мая 1974 года ОКБ ЭМ под названием "КБ энергетического машиностроения" вместе с филиалами вводится в состав научно-производственного объединения "Энергия", и Приморский филиал получает наименование Приморский филиал КБЭМ НПО "Энергия".
При выделении КБЭМ из НПО "Энергия" в 1990 году Приморский филиал оставлен в составе объединения под наименованием Приморский филиал НПО "Энергия". При создании в 1994 году Ракетно-космической корпорации "Энергия" Приморский филиал входит в ее состав в качестве дочернего предприятия — АООТ "Приморский научно-технический центр РКК "Энергия".
Руководителями предприятия в различные периоды были: Е.Н. Кузьмин — начальник филиала (1958-1969 гг.), В.Н. Антонов — и.о. главного инженера (1959-1964 гг.), Б.А. Никольский — начальник филиала (1970-1973 гг.), А.П. Андреев — главный инженер (1964-1974 гг), а затем начальник филиала (1974-1978 гг.), Б.Ф. Яковлев — главный инженер (1974-1978 гг.), В.В. Елфимов — директор (1978-1993 гг), В.В. Кузнецов — главный инженер (1979-1994 гг.). В 1993 году директором филиала был назначен С.К. Петров, а его первым заместителем Ю.В. Сидельников.
Разработка и освоение технологий работ с компонентами ракетных топлив, ранее не применявшихся в отечественном, а в большинстве случаев и в мировом двигателестроении (газообразный и жидкий фтор, пентаборан, аммиак, высококонцентрированная перекись водорода, синтин и др.), появление новых образцов ракетной техники, подлежащих отработке и испытаниям (от экспериментальных камер сгорания тягой 500 кгс для отработки процесса воспламенения и горения фтора и моноокиси фтора с диэтиламином или аммиаком до объединенной двигательной установки орбитального корабля "Буран", включающей в себя 48 отдельных двигателей и ряд других сложных систем), требовали непрерывного совершенствования и развития как самой испытательной базы, так и служб и производств, обеспечивающих ее функционирование. Так, в 1958-1968 гг. на предприятии были построены и введены в эксплуатацию стенды 12, 11, 101, 200 для отработки широкого класса двигательных установок и их агрегатов на различных компонентах топлив (жидкий и газообразный фтор, пентаборан, высококонцентрированная перекись водорода, аммиак и др.), а также сооружения вспомогательного производства. Часть стендов в ходе дальнейшей эксплуатации неоднократно реконструировалась и дооснащалась для выполнения новых задач. Период наиболее интенсивного строительства на предприятии связан с подготовкой объединенной двигательной установки орбитального корабля "Буран", когда в 1981-1986 гг. были построены и введены в эксплуатацию сооружения уникального стендового комплекса В-1, включавшего в себя закрытый вертикальный стенд для огневых испытаний ОДУ и разгонных блоков с суммарной тягой двигателей до 50 тс, работающих на жидком кислороде и углеводородном горючем (РГ-1, синтин и др.), монтажно-испытательный корпус, корпус регистрирующей и обрабатывающей аппаратуры и другие сооружения.
В результате выполненного строительства и реконструкции сооружений и систем к началу 90-х годов предприятие превратилось в уникальную испытательную базу, располагающую:
■ промышленной площадкой (158 га) с выходом на берег Финского залива;
■ четырьмя стендовыми комплексами, предназначенными для выполнения огневых и "холодных" испытаний ракетных двигателей тягой до 100 тс на жидком кислороде и углеводородных горючих, испытаний объединенных двигательных установок космических аппаратов и разгонных блоков, автономных испытаний отдельных узлов и агрегатов двигателей и ДУ;
■ санитарно-защитной зоной без постоянного проживания людей в радиусе около 5 км (7791 га) вокруг площадки предприятия;
■ надежным (по 1-й категории) электроснабжением, автономным отоплением, шоссейными и железнодорожными подъездными путями, очистными сооружениями, телефонной и телеграфной связью и др.;
■ развитой производственной инфраструктурой, обеспечивающей функционирование испытательной базы (пожарной и войсковой охраной, металлообрабатывающим и сварочным производствами, химическими лабораториями, автотранспортом, складскими помещениями, службами охраны окружающей среды — метрологической, технологической и др.);
■ опытными кадрами испытателей и других специалистов, способных решать самые сложные задачи по подготовке и проведению испытаний изделий ракетно-космической техники.
Наряду с развитием производственно-испытательной базы предприятие активно развивало строительство жилья для своих сотрудников в г. Приморске и пос. Ермилово (соответственно на расстоянии 18 и 6 км от предприятия), детских садов, гостиницы, больницы, поликлиники, спорткомплекса, инженерных сетей в жилых микрорайонах предприятия.
В течение 1958-1994 гг. предприятием построено: 19 жилых домов на 1106 квартир, общежитие для малосемейных на 95 квартир, три детских сада, магазины, поликлиника и больница, котельные с мазутохранилищами и отопительными сетями, линии электропередач с подстанциями понижения, очистные сооружения с канализационной сетью, стадион с культурно-спортивным комплексом, спецгородок для размещения войсковой охраны (в том числе казарма, здание штаба, клуб-столовая, гараж, склад ГСМ, магазин). Часть построенных объектов находится на балансе предприятия, другая передана в ведение муниципальных властей или находится в стадии оформления такой передачи.
Приморский НТЦ сыграл решающую роль как единственная в стране база в отработке ракетного двигателя 11Д14, использующего в качестве окислителя фтор или моноокись фтора. Работе непосредственно с двигателем 11Д14, который до настоящего времени остается единственным в мире образцом отработанного двигателя такого класса, использующего в качестве компонентов топлива жидкий фтор и аммиак, в Приморском филиале предшествовал этап многочисленных экспериментов по освоению технологии работ как с упомянутыми выше, так и с другими агрессивными и высокотоксичными компонентами (гидразин, несимметричный диметилгидразин, диэтиламин, пентаборан, высококонцентрированная перекись водорода).
Параллельно с испытаниями двигателей в течение 1959-1976 гг. велась отработка их отдельных узлов и агрегатов, работающих в среде жидкого фтора. За время полной отработки двигателя 11Д14 (и предшествующих его модификаций 8Д21 и 11Д13Ф) с августа 1963 по апрель 1977 года было проведено 1610 огневых испытаний на 700 экземплярах двигателей. Двигатель 11Д14 был принят КБ прикладной механики (главный конструктор М.Ф. Решетнев) для установки на разрабатываемый этим КБ разгонный блок 11С813. С прекращением работ КБПМ над созданием РБ 11С813 в 1976 году в Приморском филиале закончилась "фторная" тематика.
За время с 1953 по 1976 год коллектив специалистов (выросший с 10 "пионеров" до 1500 человек) проделал уникальную работу по освоению технологии обращения с фтором и его использованию как компонента топлива в изделиях ракетно-космической техники. Через хранилища и стенды предприятия прошли тысячи тонн жидкого и газообразного фтора. В ходе работ испытателями был найден и реализован целый ряд оригинальных технологических решений, подтвержденных свидетельствами об изобретениях; среди них наиболее значительны:
■ внедрение рецикла (повторного использования) газообразного фтора на испытательных стендах;
■ использование побудителей — ВРД в системах нейтрализации газов, вытекающих из сопла работающих двигателей;
■ отработка технологии предварительной холодной пассивации металлических поверхностей;
■ отработка технологии переохлаждения аммиака;
■ отработка технологии нейтрализации фтористого водорода, находящегося в выхлопных газах двигателя, и др.
Самый значительный вклад в работы по фторной тематике внесли В.Е. Руденко (руководитель работ до 1975 года), В.В. Кузнецов, В. А. Пинчук, А.В. Шилов, Б.Б. Новичков, А.В. Тимофеев, А.П. Андреев, Н.С. Чернов, В.В. Фокин, Ю.П. Степанов, В.В. Васильев, А. А. Мееров и др.
Следующей крупной работой Приморского НТЦ явилась стендовая отработка двигателя 11Д123, разработанного КБ "Энергомаш" (главный конструктор В.П. Радовский), являющегося маршевым двигателем II ступени РН "Зенит". Огневые испытания начались с испытаний прототипов двигателя (2УК2) в июне 1978 года и продолжались до ноября 1991 года, когда были сданы в эксплуатацию пять двигателей, предназначавшихся для проведения летно-конструкторских испытаний и штатных запусков РН "Зенит". За указанное время было проведено 411 огневых испытаний 192 двигателей. В ходе испытаний была экспериментально проверена работоспособность двигателя при замене штатного горючего РГ-1 синтином. Прирост удельного импульса тяги при этом составил 6 единиц. Была отработана и неоднократно подтверждена технология очистки двигателей такого класса от остатков горючего без разборки после контрольно-технологического испытания.
При подготовке стенда и в ходе работ с двигателем 11Д123 испытателями, конструкторами и технологами предприятия был сделан и реализован целый ряд оригинальных разработок и усовершенствований стендовых систем, среди них:
■ конструкция газовыхлопного тракта, обеспечивающая необходимое разряжение на срезе сопла двигателя, дожигание СО до СО2 в струе выхлопных газов за счет эжекции окружающего воздуха (а не впрыска кислорода, как это делается на традиционных стендах) и минимальное образование окислов азота;
■ применение стендовых пусковых емкостей, связанных с основными расходными емкостями по газовой полости и позволяющих сохранять на стенде штатную длину питающих двигатель магистралей;
■ система быстрого захолаживания горючего в стендовом расходном баке путем впрыска в бак жидкого азота;
■ конструкция термовакуум-камеры для выполнения послепусковой очистки внутренних полостей двигателя без его разборки;
■ система дистанционной тарировки тягоизмерительного устройства;
■ эффективная система автоматического пожаротушения при аварийном исходе испытания;
■ метод и автоматическое обеспечение обработки быстроменяющихся параметров (вибраций и пульсаций) на универсальных цифровых вычислительных машинах;
■ математическое обеспечение и технология автоматической обработки результатов измерений и машинного выпуска протокола испытания;
■ система автоматизированной тарировки стендовых расходных баков и др.
Наибольший вклад в работы по испытаниям двигателей 11Д123 внесли В.В. Кузнецов, А.В. Шилов, В.Ф. Суворов, И.М. Устинов, Г.Н. Изюмов, В.П. Хомутников, С.В. Минашкин, С.К. Петров, В.А. Шварев, Ю.В. Сидельников, В.В. Щиплецов, Б.Ф. Луковников, В.А. Трунцов, Н.А. Кошелев, Б.Г. Язиков, А.Е. Николаев, Е.В. Журавлев, Г.Н. Кононов, А.В. Тимофеев, С.М. Андрюшкин, В.В. Макаров, В.А. Яковлев, Л.А. Петрова и др. Активные и напряженные работы проведены Приморским НТЦ при испытаниях двигателей, агрегатов и систем орбитального корабля "Буран". Ресурсные испытания двигателей 11Д58М разработки НПО "Энергия" проводились на реконструированном после окончания работ с двигателем 11Д14 стенде в период с декабря 1978 по июнь 1982 года. Целью испытаний была проверка работоспособности двигателя в горизонтальном положении продольной оси и при повышенных режимах его эксплуатации по числу включений и длительности непрерывной работы. Всего за указанное время было проведено 222 испытания на 11 двигателях. Максимальная наработка одного двигателя составила 13 566 с при 35 включениях. Максимальная продолжительность одного включения определялась возможностями стенда и составляла 1200 с. Горизонтальное положение продольной оси двигателя при запуске потребовало внесения некоторых корректировок в конструкцию двигателя (ранее двигатель испытывался только при вертикальном положении).
Конструкторско-доводочные испытания двигателя 17Д12 разработки НПО "Энергия" проводились после завершения испытаний двигателя 11Д58М, в период с мая 1985 по сентябрь 1988 года. Целями испытаний были подтверждение работоспособности двигателя при работе на синтине, выбор циклограммы работы стендовой автоматики для обеспечения надежного запуска двигателя, проверка работоспособности двигателя в горизонтальном положении при работе на пониженном (генераторном) режиме.
Всего за время выполнения этой программы было проведено 114 испытаний на шести двигателях, суммарная наработка по времени составила 22 311 с. Положительные результаты этих испытаний позволили с большой степенью уверенности перейти к выполнению программы огневых испытаний ОДУ 17Д11, в составе которой в качестве двигателей орбитального маневрирования используются двигатели 17Д12.
После окончания этой серии испытаний в предвидении дальнейшего развития темы "Буран" и с учетом ограниченных возможностей испытательной базы НПО "Энергия" в Калининграде Московской области была начата реконструкция стенда с целью создания двух дополнительных вертикальных рабочих мест для огневых испытаний двигателей 11Д58М и 17Д12. Однако в связи с прекращением финансирования темы "Буран" реконструкция не завершена.
Наибольший вклад в подготовку и проведение испытаний двигателей 11Д58М и 17Д12 внесли В.И. Федотов, В.П. Тепляков, Е.Д. Поднозов, Г.Н. Кононов, В.Д. Кайдан, И.К. Константинов, В.И. Волков и др.
Подготовка и проведение испытаний объединенной двигательной установки ОК "Буран" (ОДУ 17Д11) явились наиболее значительной вехой в жизни испытательной базы как по требуемому техническому дооснащению, так и по сложности технических задач, вставших перед испытателями. Началу испытаний предшествовало строительство и оснащение нового стендового комплекса В-1, включающего в себя вертикальный стенд с огневым боксом и монтажными отделениями, пультовую для размещения аппаратуры управления, монтажно-испытательный корпус, корпус для размещения регистрирующей и обрабатывающей аппаратуры, газобаллонную станцию на 470 м
3 сжатых газов, хранилище синтина, корпус вакуум-откачного оборудования и целый ряд других сооружений и систем.
Испытания проходил стендовый вариант ОДУ 17Д11 — установка ЭУ 597, заключающая системы ОДУ в жесткий цилиндрический каркас с тремя выносными блоками двигателей управления. Испытания проводились под руководством межведомственной комиссии под председательством В.В. Елфимова при непосредственном участии руководителя разработки ОДУ Б.А. Соколова.
Основной целью комплексных огневых испытаний было подтверждение работоспособности всех систем ОДУ 17Д11 при совместном функционировании в ходе выполнения полетных программ ОК "Буран" и при межполетном обслуживании. Эта общая цель разбивалась на ряд частных задач (начиная с контроля чистоты внутренних полостей баков до наработки ресурса эксплуатации сверх гарантированного), испытания выполнялись по этапам, определявшимся поступлением материальной части.
■ ЭУ 597 № 10С — с июня 1986 по февраль 1987 года.
Испытания закончились аварийно: пожаром была уничтожена установка ЭУ 597 и существенно поврежден стенд. Цели испытания были выполнены лишь частично.
■ ЭУ597 № 12С — с сентября 1987 по апрель 1988 года.
Испытания прошли успешно: была отработана программа работы систем ОДУ при первом полете ОК "Буран".
■ ЭУ 597 № 31Л — с июня по декабрь 1988 года.
Программа испытаний успешно выполнена, дополнительные испытания доработанных конструкций БГО подтвердили их надежную работоспособность. Результаты этих испытаний позволили Государственной комиссии дать разрешение на выполнение первого полета ОК "Буран".
■ ЭУ 597 № 11С — с января 1991 по март 1993 года.
Программа испытаний выполнена, экспериментально подтвержден ресурс работоспособности ОДУ в 3-4 раза превосходящий полетный. В связи с прекращением финансирования темы "Буран" испытания ОДУ 17Д11 остановлены.
■ ЭУ 597 № 11С была переведена в режим хранения на стенде В-1 с периодической проверкой функционирования агрегатов до мая 1995 года, когда по решению РКК "Энергия" начаты работы по окончательной очистке полостей установки от остатков синтина и ее консервации для дальнейшего хранения вне стенда.
В период подготовки и проведения испытаний ОДУ 17Д11 специалистами предприятия предложено и реализовано множество неординарных решений, направленных на обеспечение технических условий при проведении испытаний — повышение безопасности, повышение информативности и т.д. Наиболее значительные из них:
■ технология получения больших количеств глубоко переохлажденного кислорода (до -215°С) с помощью испарения бинарных смесей (кислород+азот);
■ доработка конструкции огневого бокса, позволяющая проводить испытания при вертикальном и горизонтальном положениях базового блока ЭУ 597;
■ система эжекции, воспроизводящая в достаточной степени условия штатной эксплуатации ОДУ в космосе;
■ система автоматического газового и пожарного контроля и предупреждения;
■ система азотного пожаротушения;
■ система регистрации, контроля и обработки информации (на базе универсальных и персональных ЭВМ, объединенных в локальную вычислительную сеть) управляющих команд, выдаваемых на объект испытания и в систему управления, и др. В процессе подготовки испытаний ОДУ 17Д11 наиболее значительный вклад в их успешное выполнение внесли В.В. Елфимов, В.В. Кузнецов, Н.С. Чернов, Е.А. Баранов, О.И. Измаков, А.Н. Байчиков, Б.С. Коровкин, Н.М. Козлов, В.В. Макаров, В.И. Федотов, Ю.В. Сидельников, В.А. Трунцов, Н.А. Савин, В.В. Щиплецов, В.А. Мельникова, С.И. Логутенко, Г.Н. Головинский, А.Н. Зилитинкевич, В.М. Галяпин, И.М. Устинов, Е.В. Журавлев, Ю.В. Никонов, И.К. Константинов, А.В. Тимофеев, О.М. Андрюшкин, Н.Г. Пинчук, Л.И. Сорокина и др.
В условиях сокращения заказов на выполнение традиционных для предприятия работ по испытаниям изделий ракетно-космической техники руководство и коллектив предприятия принимают меры по сохранению достигнутого потенциала и развитию новых, нетрадиционных, в том числе конверсионных направлений деятельности. Первоочередной задачей Приморского НТЦ является сохранение имеющейся материальной базы предприятия. Реализация этого направления достигается путем осуществления поэтапной консервации стендовой базы и, в первую очередь, сооружений и систем стендовых комплексов. В течение 1994-1995 гг разработаны концепция поэтапной консервации, регламент по консервации систем и сооружений базы, график консервации систем, зданий и сооружений, не задействованных в остающихся экспериментальных работах.
Вместе с тем на ряде сооружений созданы пять новых рабочих мест для испытаний общепромышленной запорной арматуры (давление — до 25 кгс/см
2 на воде и до 1500 кгс/см
2 на воздухе, расход воды — до 400 л/с). На стенде 101 в 1991-1993 гг. введены в эксплуатацию два рабочих места для огневых испытаний высокотемпературных реакторов, предназначенных для экспериментальной отработки технологии уничтожения токсичных и экологически особо опасных веществ. Эти работы проводятся Приморским НТЦ совместно с РКК "Энергия" и Балтийским государственным техническим университетом.
Учитывая выгодное географическое положение, развитую производственную инфраструктуру и опыт коллектива, Приморский НТЦ привлекают к участию в реализации проекта "Морской старт". Концепция международного проекта "Морской старт" (Sea Launch) предусматривает необходимость создания на территории Российской Федерации берегового комплекса, предназначенного для накопления, хранения и погрузки на корабли-транспортировщики блоков РН, компонентов ракетного топлива и сжатых газов и проведения автономных и комплексных испытаний оборудования, систем стартовой платформы и сборочно-командного судна. В качестве места размещения берегового комплекса выбрана промышленная площадка Приморского НТЦ РКК "Энергия" с учетом использования по прямому назначению имеющихся сооружений и систем испытательной базы, а также местонахождения последней на берегу Финского залива. Решением задачи создания берегового комплекса в течение 1995-1997 гг. могут быть загружены до 90% производственного персонала, основные мощности производственных служб и значительная часть систем и сооружений испытательной базы.
Проект причального комплекса для обеспечения программы "Морской старт" в течение 2,5-4 лет может быть расширен с целью создания сухогрузного терминала, оснащенного складскими помещениями, грузовыми кранами и зоной отработки коммерческих грузов (II этап на причальном комплексе).
Третьим этапом планируется строительство комплекса сооружений для перевалки на морские суда сжиженных горючих газов пропан-бутановых фракций.
Приморский НТЦ может быть использован в создании комплекса сооружений для перевалки и распределения сжиженных углеводородных газов с оборотом до 0,5 млн. т в год. С проблемой создания полноразмерного сухогрузного терминала увязывается перспективная работа по строительству в пределах оформленного землеоотвода Приморского НТЦ сооружений по накоплению и распределению сжиженных углеводородных газов для их транспортировки по железной дороге и морским путем.
В 1995 году Приморским НТЦ представлены технические предложения по созданию на промышленной площадке предприятия опытно-промышленной установки по отработке технологии получения стирола (до 10 тыс. т в год) методом окислительного метилирования толуола, более экономичного по сравнению с традиционными способами. Разработчик метода — Всероссийский НИИ органического синтеза.
Одной из перспективных народнохозяйственных задач федерального значения является создание в Приморском НТЦ завода по производству сжиженного природного газа (сжижение газа, подаваемого по трубопроводам).
Рассматривается возможность привлечения Приморского НТЦ к испытаниям и отработкам энергоустановок народнохозяйственного назначения (электрохимических генераторов на основе фосфорно-кислых топливных элементов), разрабатываемых РКК "Энергия".
Приморский научно-технический центр, прошедший путь от землянок и кустарных лабораторий до создания уникальных стендовых комплексов, давший "путевку" в космос двигателю современного носителя "Зенит" (II ступень) и ОДУ орбитального корабля "Буран", накопивший за годы работы мощный технический потенциал, к концу 1995 года оказался в тяжелом положении из-за сворачивания многих космических программ. Практическое отсутствие новых разработок двигателей приводит к тому, что потенциал Приморского НТЦ остается невостребованным. Тем не менее, коллектив предприятия, заметно поредевший в последние годы, не только сохраняет в боевом состоянии стендовые комплексы, но и ведет работы по созданию комплекса "Морской старт".
8. Завод экспериментального
машиностроения.
Промышленное строительство
и социальное развитие
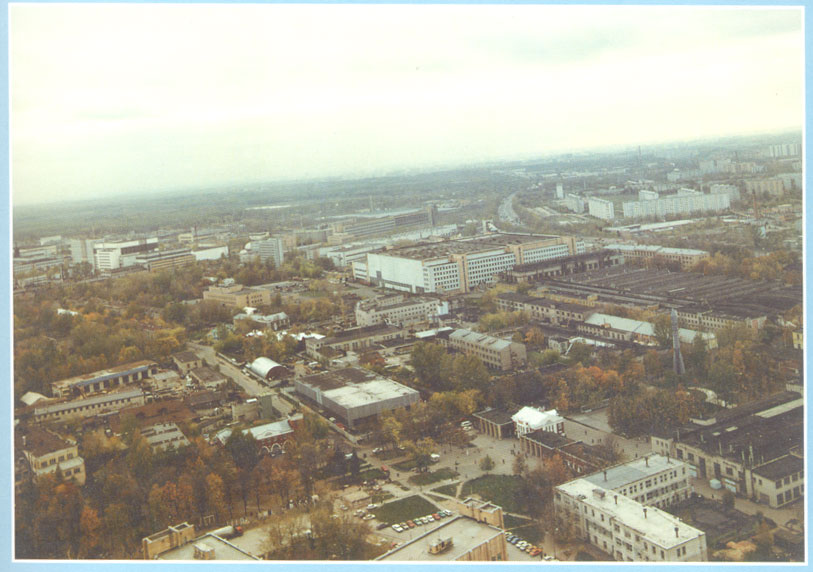 |
|
Деятельность завода в период с 1946 по 1995 г.
Опытный завод, его становление в процессе создания ракет Р-1 и Р-2 (1946-1952 гг.)
Как было сказано ранее, история Завода экспериментального машиностроения как ракетного завода начинается с 1946 года.
Постановлением от 13 мая 1946 года создается Опытный завод 88 на базе артиллерийского завода 88, который в первые годы является основой организованного согласно этому же Постановлению НИИ-88, с задачей создания реактивного вооружения.
Период становления завода был одним из самых трудных в его истории. За очень короткий срок необходимо было создать экспериментальную базу и перестроить работу завода в расчете на освоение новой техники. В конце 1946 года директор завода А.Д. Калистратов, исполнявший обязанности директора формируемого НИИ, издает приказ, в котором намечены мероприятия по разработке структуры и определению тематики.
В июле 1946 года начались строительные работы по восстановлению корпуса 2 (во время войны при бомбежке была разрушена крыша) и переоборудованию его под производство ракет дальнего действия. В это же время большая группа инженерно-технических работников и рабочих командируется в советскую оккупационную зону Германии, в том числе главный технолог С.Н. Курдин, главный металлург В.Н. Иорданский, заместитель директора завода Н.Я. Андреев, начальники цехов М.И. Пушкарев и В.Н. Иванов.
Перед командированными специалистами ставились задачи:
■ изучение материальной части ракет А-4 (Фау-2);
■ ознакомление с организацией производства ракет;
■ изучение технологии производства ракет;
■ создание технологической документации.
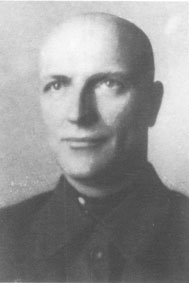
П.И. Малолетов |
В ноябре 1946 года директором завода — заместителем директора института по производству — назначается П.И. Малолетов.
Быстрыми темпами идет реорганизация производства. В корпусе 1 образовывается механообрабатывающее производство для всего завода в составе цехов 1, 3, 4, 6, 8. Начальником производства назначается Т.Я. Белоконев. Здесь же организуется корпусное производство в составе цехов 7, 9, 17; в цехе 7 разворачивается сборка зенитных ракет типа "Вассерфаль".
В конце 1946 — начале 1947 г, возвращаются командированные в Германию специалисты, поступает на завод оборудование, технологическая оснастка, инструмент, детали и собранные узлы, документация и другие материалы для проведения работ по ракетной технике.
Полученное оборудование и технологическая оснастка устанавливались, в основном, в реконструированном корпусе 2. Здесь в январе 1947 года были организованы цехи для изготовления и сборки узлов и агрегатов РДД: цех 41 (начальник цеха Н.А. Пшеничников), цех 42 (начальник цеха В.А. Разумовский), цех 43 (начальник цеха В.А. Селезнев), цех 44 (начальник цеха В.Н. Васин), цех 45 (начальник цеха Н.И. Сергиенко).
Начальником корпусного производства назначается М.И. Пушкарев.
В крайних пролетах корпуса 2 образовывается новый листоштамповочный цех 14 (начальник цеха Н.М. Березин). Сборочный цех 39 переоборудуется под сборку РДД. Начальником цеха назначается В.М. Курило.
В корпусе 1 создаются новый монтажный цех 81 и плазово-шаблонный цех 35.
В 1946 году было переоборудовано 3000 м
2, а в 1947 году — 14 000 м
2 производственных площадей.
Ракетная техника для всех была новой отраслью; многие специалисты нуждались в переквалификации.
Организовываются техническая учеба рабочих (800 человек) и кружки повышения квалификации, где занимались около 450 человек в 1946 году и 1464 человека в 1947 году. Обучением вторым профессиям было охвачено около 300 человек.
Для ИТР в 1947 году создаются курсы по новой технике, которые окончили 576 человек. С.П. Королев являлся преподавателем одного из курсов. Часть ИТР (157 человек) проходила повышение квалификации на высших инженерных курсах (ВИК) при МВТУ им. Н.Э. Баумана.
В 1947 году открывается Калининградский механический техникум на 600 человек для подготовки среднетехнического персонала.
Заводу 88 поручается сборка десяти ракет А-4 из деталей, узлов и агрегатов, изготовленных в Германии. Для этого потребовалось восстановить недостающую техническую документацию, оснастку, проверить детали и узлы на соответствие чертежам и техническим условиям, проверить годность технологической оснастки и инструмента, изготовить недостающие детали и узлы. Доработка и сборка трофейных отсеков производилась во вновь организованных цехах 41, 42, 43, 44, 45, после чего они поступали на главную сборку в цех 39. Сборка изделий в цехе 39 осуществлялась на монтажных тележках, установленных на рельсовые пути. Чтобы обеспечить сборку изделий А-4 в установленный срок, за каждое изделие первой партии нес персональную ответственность ведущий инженер из числа побывавших в Германии (Р.П. Парамонов, Н.А. Мальцев, С.М. Макаревич, В.В. Морозов и др.).
На завод 88 были возложены задачи изготовления корпусов отсеков ракеты, автоматики, рулевых машинок, клапанов, рулей, трубопроводов, кабельной сети, сборки агрегатов, общей сборки и проведения заводских испытаний ракеты.
В процессе работ возникали серьезные проблемы. Потребовалось освоение новых технологических процессов, ранее не применявшихся в артиллерийском производстве: литье заготовок из алюминиевых сплавов, изготовление силового набора и обшивки корпусов из прочных легированных сталей, сварка емкостей горючего и окислителя, изготовление клапанов автоматики, рулевых машинок, все виды прочностных испытаний, испытаний на герметичность, электроиспытаний и т.п. Необходимо было приобрести специальное оборудование, спроектировать и изготовить специальный инструмент и оснастку, нестандартное оборудование и стенды для сборки и испытаний узлов, агрегатов и изделия в целом, Для решения этих задач на заводе проводятся значительные организационно-технические работы по техническому перевооружению производства. В начале 1948 года главным инженером завода назначается Н.Я. Андреев. Работа по подготовке производства, в основном, проводилась коллективами отделов:
■ главного технолога (главный технолог С.Н. Курдин);
■ главного металлурга (главный металлург В.Н. Иорданский, а впоследствии П.Ф. Сердюк);
■ главного механика (главный механик А.В. Соловьев);
■ главного энергетика (главный энергетик Б.Ф. Левицкий);
■ главного архитектора (главный архитектор Г.Н. Казанский), а также цехов:
■ инструментального (начальник цеха Л.И. Селезнев);
■ ремонтно-механического (начальник цеха В.И. Иванов);
■ основного и вспомогательного производств.
На заводе в то время существовала система централизованной подготовки технологической документации, то есть разработка технологических процессов и чертежей на оснастку и нестандартное оборудование выполнялась отделами главного технолога и главного металлурга, которые несли ответственность за состояние технологии и оснастки в цехах.
Руководство завода в этот период издает ряд приказов и утверждает организационно-технические мероприятия по подготовке производства, наведению надлежащего порядка в цехах и организации специальных участков.
В литейном цехе 12 (начальник цеха Б.Н. Бубнов) организуется участок цветного литья, где с большими трудностями осваивается производство заготовок из алюминиевых сплавов. Организованный в трех пролетах корпуса 2 листоштамповочный цех не отвечал требованиям нового производства: низкие потолки, слабая освещенность, недостаток площадей. Требуемое оборудование не помещалось в цехе. По этой причине гидравлический пресс с рабочим усилием 500 тс был смонтирован в кузнечном цехе. Принимается решение о строительстве нового листоштамповочного цеха.
В одном из пролетов корпуса 2 организуется цех покрытий. Создаются лаборатории по изготовлению и испытанию клапанов (начальник Ю.Н. Розов) и лаборатория-мастерская по изготовлению и испытанию сильфонов и гибких металлических шлангов (начальник Н.М. Семенов).
К 1949 году была построена высотная часть сборочного цеха 39 с подъемным краном грузоподъемностью 15 т. Здесь собранные ракеты кантовались в вертикальное положение и устанавливались на стенд для окончательных работ. В этой же части цеха производились работы по погрузке изделий в вагоны. В конце сборочного цеха 39 создается испытательная станция с пультами дистанционного контроля систем ракеты. Первым начальником испытательной станции был И.В. Митрофанов.
Результатом большого и напряженного труда коллективов конструкторского отдела 3, завода и других подразделений института в августе — сентябре 1948 года стала первая партия ракет Р-1, которая была отправлена на полигон для испытаний.
В период работы над созданием ракеты Р-1 сформировались коллективы научно-исследовательских, конструкторских и производственных подразделений, сделаны первые шаги в организации экспериментальной и производственной баз, решены многие организационно-технические вопросы.
С 1947 года на заводе начался новый этап — создание ракеты Р-2.
Для проверки принятых решений, отработки чертежей и экспериментальных испытаний элементов ракет С.П. Королев ставит вопрос об организации экспериментального цеха. Такой цех 102 был организован в 1947 году на бывшем аэродроме в освободившемся ангаре. Начальником этого цеха назначается Г.Я. Семенов. В цехе были организованы участки: механический, медницкий, агрегатно-сборочный, сборочный, испытательный, а также участок аэродинамических моделей.
Создается конструкторско-технологический сектор, основная задача которого — разработка технологических процессов и оснастки. Опыт работы по артиллерийским системам дал возможность быстро освоить механическую обработку деталей и узлов. Однако освоение изготовления маложестких деталей из алюминиевых сплавов, медницких, клепальных и сварочных работ вызывало большие трудности. На авиационный завод при конструкторском бюро, возглавляемом главным конструктором С.А. Лавочкиным, для обучения этим работам была командирована производственно-технологическая бригада в составе 50 человек.
К середине 1948 года в цехе развернулись работы по изготовлению деталей, узлов и агрегатов первых пяти ракет Р-2Э (экспериментальных).
Отдел главного технолога завода вел подготовку производства к изготовлению ракет на заводе. Сразу же возникло много проблем: заказ и получение новых материалов, заготовок и комплектующих изделий. По инициативе С.П. Королева и во исполнение постановлений Правительства к разработке и изготовлению ракет Р-2 были привлечены организации и предприятия ряда министерств и ведомств.
Ряд материалов и заготовок поставляла авиационная промышленность, откуда заимствовались также технологические процессы термической обработки, гибки, штамповки, сварки, клепки из алюминиевых сплавов.
Технические службы завода вели большую работу по проектированию и изготовлению оснастки и инструмента. Кроме того, конструкторской документацией на изделие предусматривался большой объем испытаний: статические и динамические, в средах, температурные, стендовые холодные и горячие и другие, для проведения которых на заводе создавалась материальная часть. Были изготовлены силовая стена и пол для отдела прочности, а также аэродинамические установки. Завод принимал участие в изготовлении стендов в филиале института в г. Загорске.
Для подготовки производства ракет Р-2 на заводе проводилось техническое перевооружение и реконструкция действующих цехов, строительство новых цехов, организация новых производственных участков. С 1948 по 1952 г. были осуществлены крупные организационно-технические мероприятия. Только в 1948 году было введено в строй около 600 единиц нового оборудования, реконструирован литейный цех 12 для производства литья из алюминиевых сплавов, смонтированы плавильные и шахтные печи, автоклавы.
В конце 1949 года строятся два новых пролета листоштамповочного цеха 14 с установкой уникального оборудования — гидравлического пресса (мощностью 1000 тс) для штамповки крупногабаритных деталей, в том числе днищ баков; прессов мощностью 600 и 325 тс, селитровых ванн для термической обработки заготовок из алюминиевых сплавов. Реконструируется сборочный цех 39.
Изготовление и испытание арматуры (автоматики) организовывается по замкнутому циклу в цехе 3 (начальник цеха К.В. Живулин); там же создается отделение по изготовлению деталей, сборке и испытанию рулевых машинок.
На базе термического отделения инструментального цеха создается термический цех 38 (начальник цеха Ф.П. Никитин). Строится новый склад материалов 18 (начальник цеха В.А. Жуков).
Сборка ракет Р-2 организовывается в сборочном цехе 39, где производилась и сборка ракет Р-1. Отличие состояло в том, что все монтажные работы в отсеках были переданы в параллельный пролет цеха 39. Линия главной сборки проходила вдоль всего цеха. Ракеты собирались на тележках, передвигавшихся по рельсовым путям. В конце цеха располагалась станция для горизонтальных электрических испытаний. Вертикальные испытания проводились в новом высотном здании ("высотка"). В "высотке" был установлен стенд с пусковым столом, куда устанавливалась собранная ракета в вертикальном положении и проводились проверка прямолинейности оси ракет, ее закрутка по отсекам и электропневматические испытания. Это были заключительные операции, после чего изделие красили и грузили в вагоны для отправки на летные испытания. В организацию работ по сборке ракет Р-2 в цехе 39 много труда вложили начальник цеха В.М. Иванов, начальники участков Г.М. Марков, М.А. Лазарев, М.И. Ломакин, В.А. Климов, Т.И. Андреев и другие, начальник ОТК цеха В.Б. Козловский. В период разработки и изготовления ракеты Р-2 был осуществлен комплекс организационных мероприятий. В 1949 году работы по артиллерийской тематике были прекращены.
При ОКБ-1 в 1950 году создается экспериментальное производство с задачей отработки конструкций новых изделий. Начальником экспериментального производства назначается В.М. Ключарев. Под экспериментальное производство передается здание бывшего пружинного цеха площадью 5000 м
2. В состав производства переведены экспериментальные цехи 102 и 103, а также дополнительно организовываются два цеха:
■ механический с заготовительным участком (начальник цеха А.П. Рябов);
■ сборочный с отделением пневмогидроиспытаний (начальник цеха Г.Я. Семенов).
В середине 1951 года принимается решение об организации в г. Днепропетровске нового завода по ракетостроению с передачей ему серийного изготовления ракет Р-1, а в дальнейшем — и ракет Р-2. Для организации завода и освоения серийного изготовления ракет Р-1 в г. Днепропетровск были откомандированы на постоянную работу группа специалистов из ОКБ-1 во главе с заместителем главного конструктора B.C. Будником и группа руководящих работников завода 88 во главе с главным технологом завода С.Н. Курдиным, назначенным главным инженером нового завода.
Вместе с С.Н. Курдиным в г. Днепропетровск были откомандированы начальник ОТК завода Т.Р. Соловьев, начальник бюро сварки завода В.В. Бородин, начальник бюро сборки завода И.В. Федякин, старший инженер по изготовлению рулевых машинок П.М. Светлов, начальник цеха Г.Я. Семенов и другие. Вследствие такого решения на заводе производятся перемещения руководящих работников. Главным технологом завода назначается Н.Г Сидоров, начальником производства В.М. Рожков.
В начале 1952 года главным инженером завода становится Н.А. Лукавенко, а начальником ОТК — К.В. Живулин; в августе 1952 года директором завода стал А.В. Куранов.
Работа коллектива в период с 1946 по 1952 г. по созданию ракет дальнего действия Р-1 и Р-2 является важнейшим этапом становления завода, "пионера" освоения новой техники и новой отрасли промышленности — ракетостроения, которой суждено было сыграть важную роль в жизни страны.
В марте 1953 года директором завода назначается Ф.П. Герасимов, начальником ОТК — В.М. Ключарев, главным технологом — И.А. Устинов.
Изготовление ракет Р-5 (8А62)
Документация на изготовление ракет серии Р-5 стала поступать на завод с 1951 года. Предстояло изготовить ракеты в нескольких вариантах:
■ боевые — Р-5 (8А62), Р-5М (8К51);
■ научно-исследовательские — Р-5А, Р-5В.
Для проведения статических, динамических и других испытаний изготавливается дополнительное количество корпусов и отсеков.
В период освоения ракет серии Р-5 завод выпускал также ракеты Р-11 (8А61), ракету Р-2 и гражданскую продукцию.
К началу работ по освоению ракеты Р-5 цехами завода был уже накоплен большой опыт изготовления деталей из алюминиевого сплава АМг3. Это облегчило освоение изготовления деталей из более прочного алюминиевого сплава АМг5В, В цехе 11 (начальник цеха В.М. Митько) была освоена ковка сплава АД1. В цехе устанавливаются электрические нагревательные печи вместо мазутных, второй трехтонный молот собственного изготовления. Осваиваются ковка и штамповка алюминиевых сплавов АМг5В и АК6.
После реконструкции цех 12 (начальник цеха Б.Н. Бубнов) стал полностью обеспечивать потребности завода в литье.
Цех 12 в 1953 году освоил литье по выплавляемым моделям на специально созданном и оборудованном участке.
В цехе 14 (начальник цеха Н.М. Березин) проводится обновление оборудования, Термический участок цеха был полностью переоборудован: селитровые ванны как взрывоопасные заменены термическими агрегатами, установлены электротермические агрегаты для закалки и электропечи шахтного типа — для отжига.
Для сокращения цикла изготовления деталей и повышения производительности устанавливаются падающие молоты, позволяющие применять упрощенные литые цинковые штампы, что ускоряло подготовку производства.
Были спроектированы и изготовлены полуавтоматы для сварки листового материала длиной до 4,5 м и для сварки конических и цилиндрических обечаек по образующей диаметром от 600 до 3000 мм.
Для усиления технического бюро цеха 14 в 1954 году технологическая и конструкторская группы листовой штамповки отдела главного технолога были в полном составе переведены в цех с подчинением руководству цеха.
В агрегатно-сборочном цехе 40 (начальник цеха Н.И. Врунов) организовывается производство баков горючего, окислителя, торовых баков под перекись водорода, приборных и хвостовых отсеков. В цехе производились сварка баков, гидравлические испытания на прочность и герметичность воздухом, сборка и клепка корпусов хвостовых отсеков и изготовление трубопроводов. Производственная площадь цеха 40 увеличивается за счет пролетов, где изготавливались приборные отсеки и стабилизаторы ракеты Р-1. Производится установка оборудования: установлены стапели для сварки продольных швов в обечайках и кольцевых в баках, а также стапели для сборки-клепки панелей корпуса хвостовой части и полной сборки корпуса и стапель для механической обработки корпуса хвостовой части, под пилоны и другая оснастка. Продольные швы в обечайках и кольцевые швы в баках варились аргонно-дуговой сваркой по отбортовкам. В 1954-1955 гг. после получения двух импортных установок (из Чехословакии) в цехе перешли на автоматическую сварку.
В сборочно-сварочном цехе 8 (начальник цеха М.Т. Алексахин) изготавливались сборки из черных металлов: головные части, шаровые баллоны высокого давления, баки горючего и окислителя изделия 8А61 и другие. Некоторые сборки имели теплоизоляционные и теплозащитные покрытия. Это были новые, специфические технологические процессы, которые заводу предстояло осваивать. В цехе были смонтированы две шахтные печи для термообработки сварных конструкций. Организованы сварочные посты. Установлены станки для обкатки обечаек с нагревом и иное оборудование. По объему работ и новизне производственных процессов цех 8 оказался самой "горячей" точкой на заводе. Например, технология изготовления шаровых баллонов, нанесения теплозащитных и теплоизоляционных покрытий на головные части была совершенно новой. Впервые эти работы проводились в сборочно-сварочном цехе 8 на специально созданных участках.
На заводе практически не было специалистов по неметаллическим материалам и их применению. Внедрение неметаллических материалов потребовало значительных затрат времени и создания специальной оснастки. Неметаллические материалы в большой номенклатуре применялись не только в корпусах изделий, но и в приборах, кабельной сети, арматуре.
Для отработки и испытания арматуры организовывается новая лаборатория в первом пролете цеха 40. Процесс доводки арматуры требует температурных испытаний, испытаний в жидких и других средах, максимально приближенных к натурным условиям работы с обеспечением ресурса работы, поэтому лаборатория оснащалась специальным оборудованием, бронекабинами и др.
Рулевые машинки — механизмы высокой точности изготовления, с микронными допусками на размерах деталей. Для качественного изготовления этих механизмов и их контроля требуются оборудование высокой точности, производственные площади лабораторного типа и квалифицированные исполнители всех видов работ. Такие условия были созданы: выделены помещения с дневным освещением, установлено первоклассное контрольное оборудование, введена специальная вентиляция внутри лаборатории и изоляция от внешней среды. А главное — были сформированы комплексные бригады из высококвалифицированных рабочих и ИТР.
Были применены новые прогрессивные технологические процессы и оборудование: внедрен шевинговальный станок для отделки зубьев шестерен, введено хонингование для отделки отверстий в каленой рубашке корпуса, внедрены алмазная расточка корпусов с автоматическим режимом и автоматический контроль ротаметром для замера требующих высокой точности изготовления отверстий. Установлено испытательное оборудование: термохолодильная камера, вибростенд, вакуумная камера, балансировочная машина и др.
В приборном цехе 2 (начальник цеха М.К. Андреев) изготавливались кабели и наземные пульты разработки ОКБ-1.
В 1951 году цех 2 объединяют с экспериментальным цехом 106, а в 1958 году в связи с увеличением объема работ по приборам снова разделяют на два цеха: цех 4 (начальник цеха А.К. Распутько) — изготовление кабелей; цех 2 — изготовление приборов. Цех 2, пополненный оборудованием, работал по замкнутому циклу и обеспечивал завод приборами разработки ОКБ-1. Начальником цеха 2 назначается А.И. Штарков. Гальваническая и химическая обработка деталей и узлов, применяемых в изделиях новой техники, обеспечивалась в новом отделении цеха 78 (начальник цеха З.Г. Бучацкий), созданном в пролете между цехами 14 и 40.
Для ракеты Р-5 наиболее сложными оказались процессы химической обработки: пассивация внутренней поверхности торовых баллонов для перекиси водорода (был построен специальный участок для этой работы) и фосфатирование внутренних диаметров трубопроводов малого сечения до тех пор, пока не перешли на метод принудительной прокачки химических компонентов.
Общая сборка ракет Р-5 всех модификаций происходила в цехе 39 (начальник цеха В.М. Иванов).
В параллельном пролете цеха проводились монтажные работы на головной части, а в специально созданном стенде — монтажные работы на хвостовой части. После проведения монтажных работ эти отсеки выкатывались в центральный пролет для стыковки с другими отсеками изделия. На монтажных тележках состыкованная и установленная на жесткие опоры ракета передвигалась по железнодорожным путям для продолжения монтажных работ — установки приборов, трубопроводов, кабельной сети и др.
В конце цеха находилась контрольно-испытательная станция (начальник КИС А.Г. Зигангиров), оборудованная контрольными приборами.
На станции проводились комплексные электропневматические испытания ракет. Контрольные испытания ракет состояли из следующих этапов:
■ автономные испытания хвостового отсека;
■ так называемые "промежуточные" испытания, которые проводились в процессе сборки ракеты;
■ горизонтальные комплексные испытания собранной ракеты с помощью специального комплекта испытательного оборудования, смонтированного в пультовой станции.
Эти испытания считались сдаточными и проходили с участием представителей отдела технического контроля и заказчика.
В высотной части цеха был смонтирован стенд с пусковым столом для вертикальных электропневматических комплексных испытаний ракет.
Вертикальные испытания проводились выборочно — одна ракета от десяти с полным комплектом штатной аппаратуры, установленной на штатные места. При положительных результатах испытаний заказчик подписывал документ о приемке всей партии ракет. На этом же стенде проводился контроль прямолинейности оси ракет и соосности отсеков. Завершающими операциями были окраска, маркировка, чехление и погрузка для транспортировки.
Работа с изделиями продолжалась на технической позиции, так как некоторые приборы и агрегаты по техническим условиям устанавливались только перед стартом, например головные снаряженные части, гироскопические приборы и др.
На заводе в короткие сроки были изготовлены: макетное изделие Р-5 с переходной рамой для установки ракеты в испытательном стенде, комплект отсеков для статических испытаний, изделие для обкатки по железной дороге, изделие для отработки испытаний в КИС и первые экспериментальные ракеты.
В 1955 году директором завода назначается Н.А.Лукавенко, главным инженером — В.М. Ключарев, начальником ОТК — Ф.А. Беляев, начальником производства — В.М. Рожков.
Всего до 1956 года заводом было изготовлено 75 ракет Р-5, которые использовались для конструкторской отработки, стендовых и летных испытаний.
В июне 1956 года ракета Р-5М была принята на вооружение и передана для серийного изготовления на завод 566 г. Днепропетровска (Л.В. Смирнов).
Изготовление ракет Р-11 (8А61) и Р-11ФМ
Документация для изготовления ракет начала поступать на завод в 1951 году. Конструкция ракеты Р-11 значительно отличалась от конструкций ракет Р-1 и Р-2 по размерам и применяемым материалам.
На заводе в 1951 году был организован цех 5 (начальник цеха Г.А. Холин) для изготовления двигателей и второй сборочный цех 7 (начальник цеха М.П. Трубников) для общей сборки ракет Р-11 (8А61), Р-11ФМ и др.
Общая сборка ракет Р-11 и Р-11ФМ осуществлялась на площадях цеха 7. После стыковки отсеков производились монтажные работы и испытания.
В 1955 году изготовление ракет Р-11ФМ было передано с завода 88 на завод 385 в г. Миасс (В.Н. Коновалов).
Изготовление ракет Р-7
Еще в начале разработки новой ракеты Р-7 было ясно, что габариты ракеты будут превосходить габариты предыдущих ракет.
При технологической проработке, на стадии проектирования конструкторской документации, было определено, что производственные площади и высоты существующих цехов завода недостаточны для изготовления и сборки крупногабаритных агрегатов ракет Р-7.
Перед запуском в производство и в начальный период изготовления этой уникальной ракеты на заводе были проведены большие организационные и технические мероприятия.
Принимается решение начать в 1953 году строительство новых производственных площадей. Так, к корпусу 2 с северной стороны в 1956 году были пристроены пять новых пролетов длиной по 120 м, шириной 20 м, высотой 19 м (до подкрановых путей 14 м) с бытовыми помещениями. В двух крайних пролетах организовывается новый цех 41 (начальник цеха С.К. Колтунов) для изготовления топливных баков изделия. В первом пролете создается новый специализированный цех 1 (начальник цеха И.В. Поваров) для изготовления головных частей с нанесением теплозащитных покрытий. Средние два пролета были отданы цеху главной сборки 39 (начальник цеха В.М. Иванов) под сборку боковых блоков ракеты. В это же время строится новая высотная часть сборочного цеха 39, длиной 72 м, шириной 40,5 м и высотой 54 м с тамбуром длиной 60 м, высотой 19 м и трехэтажными бытовками.
Высотная часть предназначалась для сборки и испытаний ракет в "пакете", а в бытовых помещениях первого этажа разместили оборудование контрольно-испытательной станции. В тамбуре была построена малярная камера для покраски блоков ракеты. В этом же тамбуре осуществлялась погрузка ракеты в железнодорожные вагоны для отправки на полигон.
Подверглись реконструкции и переоснащению цехи завода, были установлены новое стандартное и нестандартизированное оборудование, технологическая оснастка. Подготовка производства ракеты Р-7 проводилась параллельно с разработкой технической документации в ОКБ-1.
Для ракеты Р-7 вся оснастка, кроме универсальной, создавалась заново. Было спроектировано и изготовлено большое количество технологической оснастки, инструмента, штампов, пресс-форм и многое другое. Только командной оснастки для механической обработки, сварки и т.п. было изготовлено более 3000 наименований. Проектировались и изготавливались крупные сварочные установки, несколько десятков сборочных стапелей, стенды для главной сборки и настройки антенн, многочисленная оргоснастка и стенды обслуживания, монтажно-стыковочные тележки для главной сборки, колея расширилась с 750 до 1524 мм, все безрельсовые тележки оснащались обрезиненными колесами, создавались новые пульты для гидравлических и пневматических испытаний, для отработки и испытания арматуры (автоматики). В подготовке производства ракеты Р-7 кроме инструментального цеха 28 (начальник цеха Л.И. Селезнев) участвовали все цехи как вспомогательного, так и основного производства.
Большая помощь заводу в подготовке производства и освоении новых технологических процессов была оказана отраслевыми технологическими институтами, организациями и предприятиями оборонной и авиационной промышленности и других отраслей. Высокие требования конструкции, применение новых материалов обусловили необходимость разработки и освоения множества новых технологических процессов. В каждом цехе завода велась напряженная работа по решению ряда сложных технологических и производственных проблем. Особенно следует отметить коллективы отделов главного технолога и главного металлурга, цеховых технологов, производственных мастеров и передовых рабочих.
В литейном цехе 12 осваиваются новые технологические процессы литья, в том числе изготовление отливок из нержавеющих сталей и корпусов рулевых машин. В кузнечно-штамповочном цехе 11 были освоены техпроцессы штамповки деталей из сплава АМг6Т, объемная штамповка деталей из титанового сплава ВТ1, изготовление заготовок кольцевых шпангоутов большого диаметра, штамповка заготовок шаровых баллонов. Внедрена автоматизация теплового режима нагревательных печей. В процессе изготовления заготовок и деталей для ракеты Р-7 работники листоштамповочного цеха 14 (начальник цеха Н.М. Березин, его заместитель по технической части П.В. Лемешев) столкнулись с серьезными проблемами. Штамповку днищ топливных баков диаметром до трех метров пришлось осваивать из сварных заготовок, так как промышленность в то время выпускала листы шириной до 2000 мм. Впервые в промышленности осваивается технология штамповки деталей из крупногабаритных листов титанового сплава толщиной 5-6 мм, для чего были спроектированы и изготовлены специальные штампы с электроподогревом. В цехе в этот период внедряются технологические процессы изготовления сложных деталей для жидкостных реактивных двигателей. Для обеспечения работ по механической обработке после освобождения завода от выпуска гражданской продукции в первых трех пролетах корпуса 1 (северная сторона) организуется механический цех 17 (начальник цеха Ф.К. Вологуров) с доукомплектованием новым металлообрабатывающим оборудованием и оснащением. На территории цеха создается лаборатория резания отдела главного технолога. В цехе 8 осваивается сложный технологический процесс изготовления шаровых баллонов-аккумуляторов давления. В гальваническом цехе 78 внедряется новый технологический процесс глубокого химического фрезерования. Задачи изготовления, отработки и испытаний арматуры (автоматики) и рулевых машин ракеты Р-7 пришлось решать цеху 3. При создании ракеты Р-7 количество наименований арматуры было значительно больше, чем в предыдущих изделиях. Новизна, сложность и высокие требования по герметичности и работоспособности потребовали высокой культуры организации производства, дооснащения цеха и лаборатории по отработке и испытаниям арматуры (начальник лаборатории Н.А. Пшеничников) и рулевых машин (начальник лаборатории А.В. Киров). Вводятся доводочные и контрольно-выборочные испытания, испытания в средах, максимально приближенных к натурной работе в изделии. Лаборатория арматуры дооснащалась новейшим оборудованием для снятия характеристик — специальными пультами, стендами, приспособлениями.
В цехе 5 проводится большая работа по перепланировке и дооснащению под производство жидкостных рулевых двигателей ракеты Р-7. Реконструирован стенд для гидравлических испытаний, освоены сложные технологические процессы формообразования деталей корпусов двигателей, новые процессы сварки и пайки.
В новом цехе 41 проводится большая работа по подготовке производства, оснащению и изготовлению топливных баков ракет. Для кольцевой сварки баков на базе крупного токарного станка "Кревен" создается уникальный сварочный агрегат для автоматической сварки со специальными приспособлениями, разжимными и подкладными кольцами и сварочными головками. Для проведения гидравлических и пневматических испытаний крупногабаритных емкостей (баков) спроектированы, изготовлены и установлены испытательные и тарировочные стенды. Высокие требования по чистоте внутренних полостей баков обеспечиваются специальными установками для проливки и просушки баков.
В агрегатном цехе 40, после организации производства топливных баков в цехе 41, изготавливались крупногабаритные клепаные агрегаты — хвостовые и приборные отсеки, трубопроводы разных диаметров, тоннельные трубы, сильфоны, компенсаторы, держатели для приборов, арматуры и др. Здесь же устанавливаются специальные кабины для испытаний и новое оснащение.
Вновь созданный цех 1 предназначался для освоения и изготовления деталей из неметаллов и теплозащитных покрытий, некоторые из этих материалов ранее в промышленности не применялись. Особо сложной проблемой оказалось освоение и изготовление теплозащитного покрытия головной части ракеты Р-7.
Разрабатывались новые технологические процессы, в цехе были установлены шахтные печи с вакуумными устройствами для прижатия теплозащитного покрытия к корпусу в процессе полимеризации. В освоении неметаллических материалов принимали участие многие организации и предприятия.
Сборочный цех 39 к началу производства ракеты Р-7 уже накопил определенный опыт сборки ракет. Участками цеха руководили опытные производственники-сборщики. Весной 1956 года в цехе 39 собирается первая макетная ракета Р-7 в составе центрального блока и пристыкованного к нему одного бокового блока. В цех 39 стали поступать сборочные стенды, в том числе для сборки рулевых агрегатов, пневмоиспытательное оборудование, монтажные тележки широкой колеи с тремя степенями свободы и большой грузоподъемностью, грузоподъемные средства и средства обслуживания. Первыми собирались стендовые блоки: центральные А и боковые Б, для огневых стендовых испытаний. В филиале института НИИ-88 (г. Загорск) для проведения стендовых испытаний создается испытательный стенд с монтажным корпусом. Всего в 1956 году было изготовлено по два комплекта блоков А и Б для стендовых испытаний и три макетных ракеты для макетной отработки. Одновременно велись работы по изготовлению первой летной ракеты. Цех был доукомплектован рабочими и инженерно-техническим персоналом. Создавались новые участки по сборке блоков, головных частей и т.д.
При освоении технологии сборки ракет встретилось много технических сложностей. Трудоемким оказался монтаж внутрибаковых систем. Сложными были операции по стыковке крупногабаритных и нежестких отсеков, по сборке рулевых агрегатов с жидкостными управляющими двигателями, которые требовали большой точности. Для обеспечения высоких требований к геометрическим параметрам ракеты был впервые разработан и внедрен метод обмера (контроль) отдельно блоков и сопряжения боковых блоков с центральным. В отличие от предыдущих ракет операции обмера производились в горизонтальном положении блоков. Пришлось учитывать прогиб и деформацию блоков, что обеспечило сборку "пакета" ракеты Р-7 на технической позиции в горизонтальном положении без подгоночных и контрольных работ.
К концу 1956 года первая ракета Р-7 для натурных испытаний была собрана и передана для заводских контрольных испытаний. Заводские контрольные испытания ракеты проводились на испытательном участке цеха 39.
По мере приближения передачи первой летной ракеты на электрические испытания С.П. Королев решает направить на этот участок опытных работников из ОКБ для освоения процесса испытаний, более оперативной и качественной отработки ракеты. Одним из этих работников был Д.М.Шилов, которого в дальнейшем назначили начальником контрольно-испытательной станции, а А.Г. Зигангиров стал его заместителем. Активное участие в проведении испытаний принимали: Ю.Д. Манько, Л.А. Медведев, П.М. Святский, Б.М. Афанасьев, А.Н. Андриканис, С.А. Авакимов, B.C. Иванов, И.М. Григорьев, В.И. Борисова и другие.
Контрольно-испытательную станцию для испытания ракет Р-7 планировали разместить в бытовых помещениях новой высотной части цеха 39. Однако к моменту окончания сборки первой летной ракеты работы в новой "высотке" не были закончены. Принимается решение провести эти испытания в новом монтажном корпусе филиала НИИ-88 в г. Загорске. Для этого была скомплектована бригада из испытателей цеха 39 и специалистов ОКБ-1 и института. В испытаниях принимали участие и представители по системам из смежных организаций. Были проведены автономные испытания систем и "промежуточные" горизонтальные и комплексные испытания. Работа велась круглосуточно, и к концу 1956 года ракета Р-7 была испытана и отправлена на полигон для проведения летных испытаний.
В ОКБ-1 в это время велись разработки искусственного спутника Земли.
Во второй половине 1956 года принимается решение о подключении к серийному изготовлению ракеты Р-7 куйбышевского авиационного завода "Прогресс" (директор завода В.Я. Литвинов).
Для передачи технической документации и оказания помощи заводу "Прогресс" образовываются группы специалистов: от ОКБ-1 — во главе с ведущим конструктором Д.И. Козловым, от завода — во главе с главным инженером завода В.М. Ключаревым.
Принимается решение спланировать цехи завода "Прогресс" по образу и подобию цехов завода 88.
Первые ракеты на заводе "Прогресс" собирались из деталей и узлов производства завода 88. Большая группа мастеров и рабочих завода "Прогресс" была командирована на завод 88 для освоения технологии. По мере освоения изделия завод "Прогресс" переходил на самостоятельное изготовление ракет Р-7; только элементы автоматики (арматуры) и рулевые машины еще определенное время поставлялись с завода 88. В 1956 году по итогам 10-летней работы коллективы, работающие над созданием образцов ракетной техники, Указом Президиума Верховного Совета СССР от 20 апреля 1956 года отмечаются правительственными наградами.
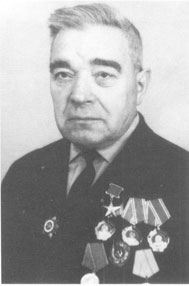
Р.А. Турков |
Среди награжденных — большая группа работников завода. Были награждены: орденом Ленина — 5 человек, орденом Трудового Красного Знамени — 26 человек, орденом "Знак Почета" — 57 человек, медалью "За трудовую доблесть" — 46 человек, медалью "За трудовое отличие" — 48 человек.
Как уже отмечалось ранее, в августе 1956 года Постановлением Совета Министров СССР ОКБ-1 (главный конструктор С.П. Королев) и завод 88 выделены из НИИ-88 в самостоятельную организацию.
Структура завода практически осталась без изменения. Директором завода и первым заместителем начальника ОКБ-1 был назначен Р.А. Турков, в прошлом руководитель крупных предприятий оборонной промышленности.
Изготовление модификаций ракеты Р-7
Для обеспечения запусков спутников Земли, межпланетных станций и других космических объектов на базе ракетного комплекса Р-7 был создан ряд модификаций ракет-носителей.
Модификация ракет Р-7 заключалась в доработке базовой ракеты Р-7 и изготовлении дополнительных ступеней (разгонных ракетных блоков Е, И и Л). Эти модификации (ракеты-носители) имели индексы 8К74, 8А91, 8А92, 8К72, 8К78 и другие в зависимости от их назначения.
Завод изготавливал материальную часть ракеты Р-7 с соответствующей доработкой. Чтобы частично разгрузить завод и оказать помощь в изготовлении материальной части, были приняты решения о поставке четырех ракет с завода "Прогресс" для модификации 8К78.
Большая нагрузка при производстве модификаций ракеты Р-7 легла на коллектив цеха 5 (начальник цеха В.Д. Вачнадзе). Этот цех выполнял задачи, связанные с громадным объемом экспериментальных работ: холодных и горячих испытаний по отработке конструкции и технологии целого ряда двигателей 8Д714, С1.5400 и других для разгонных блоков третьей и четвертой ступеней ракеты Р-7. Параллельно с выполнением производственной программы проводилась реконструкция этого цеха и модернизация оборудования.
В цехах заготовительного производства шло освоение литья и штамповок для этих двигателей из новых жаропрочных и высокопрочных материалов ЭП202Л, ЭП164 и т.п., требующее больших усилий для внедрения специального оборудования и новых технологий.
Не меньшие нагрузки испытывали и другие цехи завода, в том числе:
■ цех 41 — по изготовлению и доработке топливных баков;
■ цех 40 — по изготовлению и доработке клепаных и сварных корпусов, в том числе и для первых спутников;
■ цех 39 — по монтажным и испытательным работам в агрегатных сборках, общей сборке ракет всех модификаций и контрольным электропневматическим испытаниям.
Наряду с выполнением программы на заводе непрерывно проводилась реконструкция производства: была закончена реконструкция цеха 5, участка общей сборки и испытания арматуры в цехе 3, создан участок механической обработки неметаллов в цехе 1. Установлено новое сварочное оборудование (шовная машина МШШ-400 и две установки для сварки трубопроводов), внедрена механизированная доводка деталей арматуры, выполнены запланированные работы по подъемно-транспортным сооружениям, а также внедрены новые технологические процессы — освоены штамповка, сварка и пайка деталей из новых для завода материалов (хромистая бронза, титан и др.), внедрена гидровытяжка компенсаторов с увеличением производительности в пять раз. В работах по реализации намеченных планов ощущалась нехватка проектантов, конструкторов, технологов, мастеров и рабочих.
Изготовление космических объектов ПС-1, ПС-2, ПС-3, "Электрон", Е1 -Е7
Решение о создании спутника Земли с запуском его на орбиту в 1957 году явилось очередным импульсом к пересмотру возможностей завода.
Узким местом было проектирование и изготовление в металле технологического оснащения. Для проектирования оснастки были привлечены силы отраслевого технологического института (НИТИ-40). Создалась напряженная ситуация и с изготовлением ее в металле. Инструментальный цех 28 и участки подготовки в цехах не могли обеспечить изготовления требуемого оборудования в сроки, а разместить заказ на смежных предприятиях не удавалось. Выход из этого сложного положения был найден заместителем главного инженера завода Я.А. Лазаревичем, который внедрил на заводе универсально-сборные приспособления, обеспечившие в будущем нужды производства. Универсально-сборные приспособления собираются из нормализованных элементов; они нашли применение сначала в механической обработке деталей, а потом и в стапельной оснастке для сборки-сварки крупногабаритных ферм из трубчатых стержней и фитингов. Если для сборки УСП средней сложности требуется 4-5 ч, то на изготовление его инструментальным способом уходит 3-4 недели.
Кроме того, применение УСП создало возможность для высвобождения мощностей инструментального производства.
Создание первого ИСЗ было настолько срочным, что работы производственников и конструкторов проводились параллельно, часто доработка проводилась по эскизам от руки. Основная трудность заключалась в изготовлении сферических полуоболочек гидровытяжкой в цехе 14, их сварке со шпангоутами и полировке наружных поверхностей. На наружной поверхности не допускалось ни малейших царапин.
Полуоболочки после полировки переносились с места на место на руках и хранились на специальных подставках, обшитых мягким и чистым полотном.
Вся сварка в полуоболочках должна была быть герметичной. Качество сварных швов контролировалось рентгеном.
Герметичность собранного контейнера проверялась гелиево-воздушной смесью течеискателем ПТИ-4. Сборка и испытания на герметичность проводились в цехе 7. Особое внимание было уделено отработке системы отделения от носителя головного обтекателя и спутника ПС-1. Многократные испытания разделения проводились в сборочном цехе 39, в горизонтальном положении блока носителя (центрального блока), на монтажных тележках. Эти испытания дали возможность убедиться в надежности срабатывания пневмозамков, отделения головного обтекателя, выхода антенн из зацепления с корпусом переходника и отделения спутника от ракеты-носителя.
После успешного запуска первого спутника (ПС-1) было принято решение изготовить второй спутник — ПС-2. Завод срочно доработал носитель 8К71. Сняты были те же системы, что и на носителе 8К71 для ПС-1. Переходник был доработан: на нем установили рамы с приборами и контейнеры для собаки Лайки.
21 декабря 1957 года после запуска второго спутника ПС-2 коллективы ОКБ-1 и завода 88 были награждены Правительством орденом Ленина, а большая группа работников ОКБ-1 и завода 88 — орденами и медалями.
Завод приступил к изготовлению третьего искусственного спутника Земли — научно-космической станции (блока Д). Материалы для корпуса этого спутника были традиционные — АМг6Т и Д16Т. Материальную часть ракет 8А91 (модификация 8К71) и третьего ИСЗ изготавливали в течение второй половины 1957 и первого квартала 1958 года, За это время было сделано четыре собранных "пакета" 8А91 и были проведены стендовые испытания. Блок Д третьего ИСЗ был собран в цехе 7. Период 1957-1958 гг. богат событиями на заводе. Было принято решение Правительства о развитии базы ОКБ-1, согласно которому предусматривались:
■ пристройка к корпусу 1 пролета шириной 24 м, высотой 14 м до подкрановых путей и четырехэтажное здание бытовых помещений и лабораторий длиной 120 м;
■ реконструкция цеха 78 (бывшая котельная);
■ строительство шихтарника с западной стороны литейного цеха 12;
■ строительство машинного зала ТЭЦ на четыре турбины;
■ проводка магистрального газопровода и перевод ТЭЦ на газ;
■ комплексное строительство автобазы.
В конце 1957 года на завод начала поступать техническая документация на изделие 8К72 (модификация 8К71) и межпланетные автоматические станции, а также на изделия Е1, Е2, Е4 для исследования Луны и окололунного пространства.
С целью совершенствования структуры предприятия 3 июля 1959 года вышел приказ ГКОТ об объединении ОКБ-1 и ЦНИИ-58. После объединения вся территория бывшего ЦНИИ-58 стала называться 2-м производством по изготовлению космических аппаратов. Начальником производства был назначен Г.Я. Семенов. За счет производственной части присоединенного ЦНИИ-58 расширились возможности завода 88 в изготовлении материальной части изделий ракетно-космической тематики.
На 2-м производстве производятся полная реорганизация и реконструкция, организовываются новые цехи по тематике ОКБ-1 и перестраивается весь управленческий аппарат. Следует отметить, что значительная часть оборудования прежнего (артиллерийского) производства ЦНИИ-58 не могла быть использована для производства изделий новой техники. Не было оборудования для гидравлических, пневматических и вакуумных испытаний, а также необходимого сварочного оборудования и оборудования контрольной испытательной станции. Кроме того, необходимо было подобрать и подготовить соответствующих специалистов.
Разработка планировок вновь подключенного производства поручается заместителю главного технолога А. А. Аксенову и начальнику бюро оборудования В.И. Симакину. В этот период были организованы:
■ приборный цех 42 — наземное испытательное оборудование (начальник И.Б. Хазанов);
■ механический цех 43 — обработка деталей и сборок (начальник А. А. Зуев);
■ цех 44 — общая сборка изделий и испытаний (начальник В.С. Петров);
■ цех 45 — сборка-сварка агрегатов (начальник А.П. Неделько);
■ цех 46 — изготовление оснастки и инструмента (начальник В. А. Ермоленко);
■ литейный цех 47 (начальник А.Л. Мейтис).
В соответствии с тематикой работ приобреталось и устанавливалось оборудование. Создаются филиал отдела главного технолога (начальник П.П. Блохин) и производственно-диспетчерский отдел (начальник К.И. Демидов). Раньше других цехов показали результаты своего труда цехи инструментальный и заготовительный бывшего ЦНИИ-58, что позволило заводу в значительной степени усовершенствовать процесс подготовки производства. Высококвалифицированными кадрами пополнилось заводоуправление (плановый, диспетчерский отделы). В отдел главного технолога пришли опытные специалисты. В строительных работах по реконструкции и организации производства принимали активное участие коллективы цехов. Уже к концу 1959 года некоторые цехи (43, 45, 46) работали на полную мощность, сборочный цех 44 по существу был создан заново, поэтому его эксплуатация была начата несколько позже.
В соответствии с планом работ по изготовлению аппаратов для освоения окололунного пространства завод в 1960 году начал производить космические аппараты "Электрон-1, -2, -3, -4". Корпуса спутников Э-l и Э-ll были сварными из алюминиевого сплава АМг6; они проверялись на прочность гидравликой, а на герметичность — гелиево-воздушной смесью в барокамере. Внутри корпусов монтировались сварные рамы из магниевого сплава МА2-1, на которых устанавливалась научная аппаратура.
Тематика работ на заводе значительно усложнилась за счет изготовления космических объектов освоения окололунного пространства и поверхности Луны. Завод приступил к изготовлению межпланетных станций МС Е1, МС Е1А, МС Е2А и автоматических межпланетных станций АМС Е2, АМС ЕЗ, АМС Е4, АМС Е5, АМС Е6. Все межпланетные объекты планировалось изготавливать на 2-м производстве. Но в связи с неготовностью некоторых цехов этого производства к этим работам выпуск первых корпусов объектов происходил на 1-м производстве, цехи которого уже имели опыт изготовления первого спутника.
Межпланетные станции Е2 и Е2А по конструкции и изготовлению отличались от Е1 и Е1А. Корпуса представляли собой цилиндры диаметром 800 мм, длиной 1500 мм, соединенные с днищами сферической формы. Материал всех элементов — традиционный АМг6. Новизна была в герметичности соединений иллюминаторов с корпусами. Остальные монтажные работы не вызывали трудностей.
Изготовление космических объектов М и MB, "Зонд", "Молния"
В соответствии с решением Правительства о создании аппаратов для исследования планет Марс и Венера 28 февраля 1960 года С.П. Королев утверждает график проектирования, изготовления материальной части и проведения экспериментальных работ по автоматическим межпланетным станциям для исследования планет Марс, Венера и межпланетного пространства.
Сроки изготовления диктовались астрономическими условиями. Так, первые АМС (1М) необходимо было изготовить к сентябрю 1960 года. Завод справился с этой задачей. Строительство помещения будущего сборочного цеха 44 и контрольно-испытательной станции было еще не закончено. Бытовые помещения, в которых разместились пультовые, остались без ремонта.
В связи с этим станция 1М после проведения промежуточных испытаний и испытаний отдельных систем в разобранном виде (из отдельных блоков) была помещена в специально изготовленные контейнеры, погружена в самолет и отправлена 30 августа 1960 года на полигон. Этим же самолетом на полигон была отправлена вся необходимая наземная контрольно-испытательная аппаратура, кабели, заводская оснастка и оборудование, необходимые для проведения операций сборки, монтажа, проверки герметичности в барокамере.
В сентябре 1960 года завод приступил к изготовлению АМС для полета на планету Венера (1ВА). В течение 1961-1962 гг. завод изготавливал АМС (2MB) в четырех вариантах:
■ 2МВ1, 2МВ2 — для полета к Венере;
■ 2МВЗ, 2МВ4 — для полета к Марсу;
В 1963 году завод приступил к изготовлению серии АМС — ЗМВ.
За пять лет (1960-1965 гг.) заводом было изготовлено 19 автоматических межпланетных станций этих серий. В цехах 2-го производства изготавливались корпуса орбитальных и специальных отсеков, проводилась сварка и испытывались на прочность и герметичность изделия, Нанесение теплозащитного покрытия на корпус специального отсека (спускаемого аппарата) осуществлял цех 1. Так как опыта в нанесении таких теплозащитных покрытий у завода не было, то необходимо было освоить новую технологию их нанесения. В этой работе активное участие приняли работники цеха 1 В.И. Рыжиков, Л.С. Грачева, Ю.И. Голубин, В.И. Гречишко.
При изготовлении герметичных корпусов и рам из магниевых сплавов МА8, МА2-1 в цехе 45 возникли трудности из-за утяжки и трещин в сварных швах, деформации базовых шпангоутов после их сварки с оболочкой корпуса. Устранить эти дефекты удалось термофиксацией в специальных приспособлениях в шахтных печах, подбором режимов сварки и термообработки после сварки.
Много сил и энергии для решения этих вопросов приложили технологи Л.И. Шихолин, Т.С. Петухова, В.М. Захаров, производственные мастера А.Н. Сельдяков, А.И. Половихин и другие.
Сборка всех этих станций проводилась уже в цехе 44, а электроиспытания — в КИС 2-го производства. Сборка станций была сложной, из-за разных вариантов увеличивался объем подготовки производства.
Приходилось решать вопросы, с которыми раньше не сталкивались. Например, проблема юстировки оптических приборов ориентации относительно приборов управления с большой точностью (20"). Эта проблема решалась благодаря разработке оригинальной технологии и внедрению специального оборудования. Активное участие в решении этих вопросов принимали технологи цеха 44 В.Е. Гальперин, Е.С. Федоров и другие.
Трудности появлялись и при проведении испытаний в КИС. Так, например, происходил непроизвольный отстрел крышек парашютной системы в спускаемом аппарате, что требовало доработок и повторной сборки.
В 1964 году завод приступил к изготовлению спутников дальней связи "Молния-1". На этом изделии был применен принцип агрегатирования отдельных систем. Например, корректирующая двигательная установка, пневмосистема ориентации и коррекции, система терморегулирования представляли собой отдельные агрегаты. Каждый из них мог собираться и испытываться автономно. Все это существенно облегчало сборку изделия и сокращало цикл общей сборки объекта.
Изготовление корпусов конических днищ и других деталей и сборок, а также агрегатная и главная сборка трудностей не представляли. Сварку корпусов и их испытания проводили в цехе 45, сборку и испытания — в цехе 44 и КИС 2-го производства. Трудности возникли в процессе электроиспытаний спутника в КИС. Например, первый спутник "Молния-1" находился на электроиспытаниях свыше одного года: много было доработок приборов и систем, часто выходила из строя радиоаппаратура. Активное участие в испытаниях принимали А.Н. Андриканис, А.В. Бачурин, М.П. Василенков и другие.
Изготовление ракет РТ-1 и РТ-2
В 1960 году на завод стала поступать конструкторская документация на твердотопливную ракету РТ-1 (8К95). Твердотопливная ракета отличалась от жидкостной по компоновке и по используемым материалам: из 597 металлических деталей 33% составляли детали из черных металлов. Впервые были применены нержавеющая сталь ЭИ712, жаропрочные стали ЭИ962, ЭИ962А и титан ВТ14. Из этих металлов изготавливались основные детали двигателей: верхние и нижние обоймы, днища, сопла и фермы.
Корпуса двигателей блоков всех ступеней изготавливались из стеклопластиковых труб диаметром порядка 800 мм, заготовки труб поставлялись заводу специализированным предприятием, поковки из ЭИ961 для обойм — Кулебакинским металлургическим заводом (Горьковская область). Днища, передние и задние, штамповались из жаропрочной листовой стали ЭИ962А, сопла — из титана ВТ14. Корпуса всех отсеков были однотипные по конструкции и изготовлению (клепаные, непанелированные); в их состав входили обшивки, силовые наборы из прессованных профилей для стрингеров и шпангоутов (материал Д16Т).
Для агрегатов ракеты и общей ее сборки потребовалось изготовить 13 стапелей менее сложных, чем для других ракет. Самыми сложными и длительными в изготовлении были двигатели. Основная работа по их созданию велась в цехе 8 (начальник С.Г. Ермаков). Проблемы возникли при использовании новых материалов и освоении технологических процессов:
■ штамповки и калибровки днищ (цехи 11 и 8);
■ термообработки деталей и сварных сборок (цех 38);
■ механической обработки стеклопластиковых труб с нарезкой ленточной резьбы (цех 8);
■ изготовления графитовых вкладышей в критические сечения камер с последующей заменой их вольфрамовыми;
■ напыления раструбов сопел окисью алюминия (цех 8);
■ обеспечения герметичных соединений днищ, верхнего и нижнего, с трубой по ленточной резьбе (цех 8);
■ нанесения теплозащитного асботекстолитового покрытия на днищах и головных частях (цех 1).
Для механической обработки стеклопластиковых труб с нарезкой ленточной резьбы потребовалось провести модернизацию крупногабаритного токарного станка (удлинение станины), напыление окиси алюминия на титановые раструбы сопел. При сборке герметичного соединения днища с трубой по ленточной резьбе изготовили специальное приспособление, а для испытания соединений на прочность гидравликой — резиновые мешки для внутренних полостей труб двигателей. В цехе 8 собирались только одиночные двигатели с передачей их в сборочный цех 39; для изготовления ракеты РТ-1 потребовалось около 1000 наименований специальной оснастки.
Следует отметить слаженную работу коллектива цеха 8: начальника цеха С.Г. Ермакова, начальника технического бюро Д.Д. Мирошина, старшего мастера цеха В.В. Бухарина, главного сварщика завода Б.П. Бабанова, технологов-сварщиков Ю.Л. Яровинского, И.А. Каменецкой, конструктора отдела главного технолога С.П. Никитина. Главную сборку ракеты проводили в цехе 39, причем сборку блоков А, Б, В — на специальных стендах. В КИС цеха 39 проводили проверку электрических цепей систем и функционирования всех механизмов. Ракеты, проверенные и принятые OTK и представителем заказчика, грузили в специальные вагоны и отправляли на полигон. В 1961 году завод изготовил шесть ракет РТ-1, а в 1962 году — десять. В 1965 году ракета РТ-1 была снята с производства и началась подготовка производства новой твердотопливной ракеты РТ-2. Ракета РТ-2 (8К98) по конструкции существенно отличалась от РТ-1, и поэтому надо было вновь выполнить большой объем подготовки производства. У завода в это время не было необходимых мощностей и достаточных производственных площадей. Главный конструктор С.П. Королев предложил организовать замкнутое производство по изготовлению твердотопливных ракет на 3-м производстве предприятия. Но учитывая большой объем капитального строительства, сроки организации производства и освоения ракеты РТ-2, было принято решение о привлечении к изготовлению других предприятий.
За заводом 88 были закреплены работы:
■ главная сборка и контрольные испытания ракеты;
■ изготовление клепаных агрегатов (хвостовые и приборные отсеки);
■ изготовление головной части;
■ изготовление переходных ферм, направляющих колец;
■ изготовление поворотных сопел;
■ изготовление арматуры, трубопроводов, кабелей, ряда приборов и отдельных видов наземного оборудования.
В процессе изготовления ракеты РТ-2 так же, как и в процессе изготовления РТ-1, возникали трудности в освоении технологии производства деталей и агрегатов из высокопрочных, жаропрочных сталей и титановых сплавов.
Много проблем появилось в процессе изготовления поворотных сопел при обеспечении герметичности уплотнений и соплового вкладыша, который предполагалось выполнить из силицированного графита с покрытием внутренней поверхности вольфрамом, а также при изготовлении головной части ракеты РТ-2. Здесь основной проблемой было освоение производства теплозащитных покрытий для головной части и крышки к ней из радиопроницаемых материалов.
Практически за два года ракета РТ-2 была подготовлена к серийному производству и передана на другие предприятия отрасли.
Активное участие в подготовке и организации производства ракет РТ-1 и РТ-2 принимали Ю.И. Голубин, П.И. Кежаев, В.Д. Вачнадзе, В.М. Дубинин, A.M. Грачев, Н.В. Свиясов, В.П. Лебедев, В.С. Гаврилов, А.В. Еремин, Б.И. Колесников, В.И. Мытарев, С.М. Ососов и другие.
Изготовление ракеты Р-9
В 1960 году приступили к изготовлению двухступенчатой ракеты Р-9. Ракета состояла из блока А — первой ступени, блока Б — второй ступени и головной части. Уже к концу года были созданы: по три блока А и Б — для холодных испытаний, три блока Б и два блока А — для статических. В 1961 году завод изготовил 16 ракет Р-9, а в 1962 году — семь ракет для летно-конструкторских испытаний.
Технологический анализ ракеты при проектировании, разработке рабочей документации и подготовке производства показал, что не потребуется значительно изменять планировку производственных площадей и вводить новое оборудование. Следует отметить, что конструкция узлов ракеты допускала некоторое заимствование технологического оснащения, использованного на предыдущих ракетах. При производстве ракеты Р-9 применялись новые марки материалов (магниевый сплав МА1, сплавы АЛ8 и АЛ8У, титановые сплавы ОТ4, ВТ1, ВТ1-2, стальное жаропрочное литье ЭИ712, медный жаропрочный сплав № 11).
Внедрялись более совершенные способы изготовления трудоемких узлов: соединение днищ с обечайками топливных емкостей посредством стыковочных целиковых шпангоутов, получаемых механической обработкой из гнутых и сваренных встык заготовок, а затем — с использованием кованых колец Куйбышевского металлургического завода; химическое фрезерование; в некоторых случаях изготавливались титановые трубопроводы вместо стальных из сплава Х18Н9Т; магниевое сложное литье контейнеров под гироскопические приборы и другие узлы, биметаллические переходники (сталь-алюминий), получаемые механической обработкой из прутков и листов, сваренных методом взрыва и трением; силовой набор из стрингеров и промежуточных шпангоутов, в основном из прессованных стандартных профилей. Все это позволило снизить трудоемкость изготовления и уменьшить массу изделия. Изготовление ракеты в целом и агрегатов происходило главным образом на 1-м производстве.
Условия для испытания ракеты Р-9 на прочность и герметичность узлов, в принципе, не отличались от условий испытаний предыдущих ракет.
Применение автоматической аргонно-дуговой сварки на топливных емкостях (около 640 м сварных швов) повысило их герметичность. Конструкция клепаных отсеков позволила применить 70% прессовой клепки. Эти отсеки герметизировались герметиком У-30С и шпатлевкой Э4020.
После проведения удовлетворительных летно-конструкторских испытаний ракета Р-9 была принята на вооружение и передана в серийное производство в 1963 году на завод "Прогресс".
Изготовление кораблей ЗКА и ЗКВ
В мае 1959 года завод приступил к изготовлению космических кораблей для полета человека в космос.
Одним из важных мероприятий по обеспечению качества и надежности создания пилотируемых объектов явился выпуск в декабре 1960 года специального "Положения по ЗКА", которое определило порядок изготовления изделий типа ЗКА и их заводских испытаний.
Положение по ЗКА" предусматривало особую ответственность главных конструкторов, начальников отделов за качество конструкторской документации, руководителей завода 1 — за качество технологической документации и качество изготовления изделий, узлов и агрегатов. Оно запрещало вариантность изделий ЗКА, изменение технологии ведения сборки и испытаний изделий, применение на объекте деталей, узлов, имеющих отступления от технической документации. Узлы и агрегаты, изготовленные до выпуска "Положения по ЗКА", должны были иметь повторное заключение о допуске на объект ЗКА. "Положение по ЗКА" было принято на Совете главных конструкторов для исполнения всеми смежниками, участвовавшими в создании пилотируемых объектов, и действовало до 1968 года.
Конструктивно корпуса экспериментальных кораблей-спутников (1К) и пилотируемых кораблей — одноместных (серии ЗКА), трехместных (серии ЗКВ) и двухместных для выхода человека в космос (серии ЗКД) — были однотипными по форме и размерам, отличались, основном, составом оборудования и приборов.
Главная производственная работа по изготовлению космических кораблей была сосредоточена в цехах 2-го производства, в основном в агрегатно-сварочном (сборочном) цехе 45, монтажно-сборочном цехе 44, а также цехе 1 (нанесение теплозащиты) 1-го производства. К этому времени в цехах 14, 39, 40 заканчивается подготовка производства по укрупненной технологии и передача изготовленной оснастки и задела деталей в цехи 2-го производства. Кроме того, из цеха 40 в цех 45 переводится бригада слесарей и сварщиков.
На заводе изготавливается большое количество материальной части в виде отдельных узлов, агрегатов, установок и космических кораблей для проведения экспериментальных работ в наземных условиях. Самым трудоемким в изготовлении был спускаемый аппарат, и по длительности его изготовления определялся цикл изготовления всего космического корабля. Спускаемый аппарат состоял из металлического корпуса и наружной теплозащиты. Корпус был сварен (диаметр — 2 м) из элементов сферической и торовой формы, выполненных из листового алюминия АМг6 толщиной 3 мм. Заготовку элементов производил листоштамповочный цех 14.
Первые корпуса спускаемого аппарата в цехе 45 сваривали вручную на специальной деревянной оправке с медными вставками — подкладками в местах стыка элементов. Элементы предварительно подгоняли между собой по стыкам вручную. Отверстия для люков подкреплялись вварными шпангоутами. Внутри сваренного корпуса вваривались силовые элементы и элементы для установки и крепления оборудования и приборов. Для автоматической сварки использовался манипулятор. Протяженность швов в спускаемом аппарате составила 50 м.
Большие трудности вызвали деформации вваренных шпангоутов и дефекты в сварных швах (непровары, трещины и др.). Дефекты в сварных швах обнаруживали рентгеновским просвечиванием, которое к тому времени широко использовалось на заводе для обнаружения дефектов в сварных швах и литье. Дефекты исправляли разделкой дефектных мест с последующей подваркой. Гораздо труднее было справиться с восстановлением потерянных размеров после сварки (особенно с появлением неплоскостности). Устранение дефектов механическим способом не применялось. Термофиксация проводилась в заневоленном состоянии сварной сборки в шахтной печи, что дало положительные результаты. Обнаруживались и просчеты при изготовлении приспособления из стали. Разный коэффициент расширения материалов оснастки и спускаемого аппарата приводил к деформации. Впоследствии шпангоуты вваривали в элементы оболочки с последующей механической обработкой шпангоутов на карусельном станке. После сварки корпуса спускаемого аппарата проводили рентгеноконтроль сварных швов. Испытания на прочность водой и на герметичность гелиево-воздушной смесью проводили на участке цеха 45. Окончательный контроль герметичности корпуса спускаемого аппарата проводили в барокамере цеха 44. Если натекание гелиево-воздушной смеси в корпусе спускаемого аппарата было больше допустимой нормы, то старались найти место течи в спускаемом аппарате вне барокамеры. Приборный отсек, состоящий из верхнего и нижнего корпусов типа усеченных конусов с разъемным соединением по шпангоутам, был сварным из листового алюминия марки АМг6 и силового набора, приваренного к корпусу. Внутри корпуса размещалась силовая конструкция для установки ТДУ. Изготовление корпуса приборного отсека было несколько проще, чем корпуса спускаемого аппарата.
Приборная рама, входящая в состав приборного отсека и устанавливаемая внутри него, сваривалась из магниевых профилей, труб и фитингов (на первых изделиях из сплава марки МА8, а затем — из сплава марки МА2-1). Сварка в основном была стыковая, внахлест и насчитывала около 600 коротких швов. Главная трудность — появление трещин в зонах сварных швов. На первой раме, сваренной обычным способом, насчитывалось около 1000 трещин. В дальнейшем и эта проблема была решена.
Нанесение теплозащитного покрытия на спускаемый аппарат считалось сложной и трудоемкой операцией. Теплозащитное покрытие, предусмотренное конструкторской документацией, представляло собой пеношамот из керамических плиток, текстолитовые кольца и асботекстолит, пропитанный смолами. При этом теплозащитное покрытие по обводу было разной толщины. На первых спускаемых аппаратах толщина теплозащитного покрытия составляла в лобовой части корпуса 150 мм, а на верхней части — 30 мм. Подобные работы по нанесению теплозащитного покрытия проводились впервые в стране. Сложность этой работы усугублялась еще и тем, что корпус СА не был чисто сферическим. Сферическая верхняя часть переходила в конусную часть, а в лобовой части снова становилась сферической. Работа на первых корпусах спускаемого аппарата выполнялась в значительной степени вручную. Введение механической обработки наружного контура защиты сократило сроки изготовления до двух месяцев. Полимеризация покрытия осуществлялась в шахтной печи цеха 1, затем спускаемый аппарат с нанесенным теплозащитным покрытием направлялся в цех 44 для сборочно-монтажных и контрольно-испытательных работ.
Над задачей нанесения теплозащитного покрытия на спускаемый аппарат трудилось много специалистов предприятия. Активное участие в этой работе принимал коллектив материаловедческого отдела.
Значительную работу по организации проектирования, изготовления и внедрения специальной оснастки проводили руководители отдела главного технолога, а также начальник инструментального цеха 28 Л.И. Селезнев.
В конце 1959 года сборочный цех 44 приступил к комплектации и сборке первого корабля-спутника серии 1К. Цех 44 был ведущим и завершающим в производственном цикле изготовления космических кораблей: сюда направлялись все детали сборки и агрегаты, в том числе и от смежных организаций. В цехе была создана четкая система учета поступлений и расхода комплектующих. Для сложных и ответственных сборочно-монтажных работ на космических кораблях были привлечены в цех опытные специалисты производства В.С. Петров, Л.И. Филиппов, начальник технологического бюро Л.И. Варфоломеева, технологи В.И. Минаев, В.В. Монахов, Г.В. Суворов, М.В. Мокробородов, мастера и рабочие М.И. Воскобойников, П.Ф. Переведенцев, Ю.Д. Силаев и другие.
Цех имел следующие производственные участки: сборки тяжелых космических кораблей типа ЗКА (начальник М.И. Воскобойников), сборки межпланетных автоматических аппаратов типа "Луна-2" и "Луна-3" и экспериментальных установок для отработки изделий (начальник участка Ю.И. Лыгин), сборки и испытаний пневмоагрегатов и иллюминаторов (руководитель В.И. Меркулов), сборки приборно-агрегатных отсеков (начальник участка К.Г. Горбатенко), а также вакуумно-испытательную станцию (руководитель А.П. Ребров) и контрольно-испытательную станцию (руководитель А.Н. Андриканис). Администрация КБ и завода уделяла большое внимание организации работ в цехе 44.
Первым на техническую позицию в апреле 1960 года был отправлен корабль 1КП. На этом корабле не предусматривалось теплозащитное покрытие, для компенсации его массы на оболочку спускаемого аппарата были установлены специальные грузы — приборы 32 наименований, а в приборном отсеке — 70 наименований. На последующих кораблях серии 1К объем работ увеличивался, и уже на корабле № 6 были установлены приборы 229 наименований, из них в спускаемом аппарате — приборы 100 наименований. Определение положения центра массы проводили в цехе 39, так как в цехе 44 не было необходимого оборудования и подготовленных специалистов. Автономные и комплексные испытания кораблей-спутников серии 1К на функционирование всех систем проводились в КИС 1-го производства, где была выделена испытательная площадка в "большой высотке". Здесь на базе КИС цеха 39 создали отдельный КИС цеха 44, но испытания в основном проводились в КИС цеха 39.
Испытания первого беспилотного корабля 1КП проходили очень трудно, так как это были первые испытания сложной техники. Они проводились в КИС цеха 44. Здесь же была проведена и часть испытаний корабля "Восток", на котором совершил полет Ю.А. Гагарин. В связи с необходимостью ускорения работ по кораблю "Восток" его испытания были завершены на технической позиции. К этому времени принимается решение оборудовать на 2-м производстве стендовый корпус под КИС цеха 44. Рабочие места для кораблей располагаются в зале корпуса, а пультовые — в бытовых помещениях. В КИС цеха 44 были испытаны все корабли серии "Восток", кроме первых двух, а также все корабли серии "Восход". Активное участие в испытаниях принимали А.Н. Андриканис, А.В. Бачурин, Б.Н. Нечаев, В.В. Москвин, М.П. Василенков, А.А. Климов, О.Г. Тупицын, Н.Я. Яковенко, А.В. Ермилов, А.А. Фролов, А.Ф. Тычкин, М.А. Купцов и другие.
В эти годы (1962-1963 гг.) с целью координации работ участков КИС цехов 39 и 44 и повышения качества испытаний эти участки организационно были выведены из подчинения начальников цехов 39 и 44. Начальником КИС — заместителем главного инженера завода — был назначен Д.М. Шилов, его заместителями: участок КИС цеха 39 — А.Г. Зигангиров; участок КИС цеха 44 — А.Н. Андриканис.
На заводе была введена система работы по технологическим паспортам, создаваемым технологическими бюро цехов.
В апреле 1960 года для работы с кораблем 1КП на полигон отправляется бригада слесарей-сборщиков и испытателей, которую возглавил Л.И. Филиппов — опытный специалист по сборочно-монтажным работам.
Первым пилотируемым космическим кораблем, изготовленным заводом, был ЗКА № 3 ("Восток"), на котором 12 апреля 1961 года совершил полет Ю.А. Гагарин, а затем последовали космические корабли: ЗКА № 4 "Восток-2" (космонавт Г.С. Титов, 1961 год); ЗКА № 5 "Восток-3" (космонавт А.Г. Николаев, 1962 год); ЗКА № 6 "Восток-4" (космонавт П.Р. Попович, 1962 год); ЗКА № 7 "Восток-5" (космонавт В.Ф. Быковский, 1963 год); ЗКА № 8 "Восток-6" (космонавт В.В. Терешкова, 1963 год).
Для наземной отработки штатных кораблей-спутников 1К и ЗКА завод изготовил корабль-тренажер для тренировки космонавтов, три спускаемых аппарата для отработки парашютной системы, морской макет спускаемого аппарата для проверки плавучести корабля, спускаемый аппарат для статических испытаний, тепловой, объемный и антенный макеты, приборы для отработки систем. Все макетные агрегаты были копией основного изделия.
Корабль "Восход" отличался от кораблей "Восток" компоновкой оборудования и приборов, поэтому продолжалось изготовление корпусов без перестройки производства, однако сборочно-монтажные работы в цехе 44 были затруднены из-за изменений в компоновке корабля.
В производстве комплектующих узлов и систем космических кораблей принимали участие многие ведомства. Для своевременного обеспечения завода материалами и полуфабрикатами, а также комплектации готовыми элементами требовалась высокая организация работ. В то же время постоянно расширяющаяся программа изготовления космических объектов повлияла на формирование производственной структуры завода. Получило развитие производство функциональных узлов, приборов, антенно-фидерных устройств. Кроме приборного цеха 2 (А.И. Штарков), были образованы цех 52 — рулевых машинок, приводов и, впоследствии, стыковочных узлов (Н.А. Pay), цех 53 — антенно-фидерных устройств (Н.П. Полянский). Приборные цехи в 1963 году объединились в приборное производство (И.Б. Хазанов).
В эти же годы принимается Постановление Правительства о подключении ряда заводов к изготовлению приборов и узлов для космической техники. Большое значение имело освоение технологии изготовления приборов и аппаратуры на серийных заводах, Наибольший вклад внесли Азовский оптико-механический завод (Н.Г. Васильев, в настоящее время А.И. Накашидзе), Уфимский приборостроительный завод (Г.В. Панков, Н.А. Золотухин, в настоящее время Ю.Г. Бакланов), завод "Киевприбор" (Г.П. Баранков, в настоящее время О.Н. Лебедев), московский завод "Пластик" (И.И. Котляренко, М.Г. Демин, в настоящее время Е.К. Александров).
Изготовление кораблей "Зенит"
В 1960 году на завод поступила техдокументация на первый принципиально новый по своему назначению космический аппарат "Зенит", спроектированный на базе корабля "Восток". Изменения корпуса были небольшими: увеличены люки для иллюминаторов в спускаемом аппарате, введены цилиндрическая вставка между днищами и новая сварная рама из профилей магниевого сплава МА1. Поэтому изготовление корпусов спускаемого аппарата и приборного отсека в цехе 45 не было затруднительным, так как вся работа выполнялась в значительной мере по технологии соответствующих корпусов "Востока" и на том же оборудовании.
Главное отличие кораблей "Зенит" заключалось в бортовой аппаратуре корабля. Основная часть систем кораблей серии "Зенит" разрабатывалась специально, что определялось характером решаемых задач. В связи с этим увеличились объемы работ по подготовке производства и изготовлению комплектующих в цехе главной сборки 44 (В.И. Зудинов).
Определенные трудности возникли в связи с необходимостью транспортировки корпуса спускаемого аппарата после изготовления в цехе 45 на 1-е производство в цех 1 для нанесения теплозащитного покрытия (моста, соединяющего 1-ю и 2-ю территории, в то время не было). Затем спускаемый аппарат вновь возвращался на 2-е производство в цех 45, а затем на сборку — в цех 44. Это приводило к потере времени, поскольку одновременно шли доработки по результатам пуска.
С 1961 по 1964 г. завод изготовил по заказу Министерства обороны 15 кораблей-спутников "Зенит". В дальнейшем выпуск этих космических аппаратов был передан заводу "Прогресс".
Производственно-технологические работы по комплексу Н1-Л3
К изготовлению трехступенчатой ракеты Н1 завод приступил в конце 1960 года. Так как собранные на заводе-изготовителе ступени ракеты не могли доставляться на техническую позицию существующими средствами транспортировки из-за больших габаритов и массы, в конструктивной схеме ракеты учитывалась возможность членения отдельных агрегатов на предельно крупные транспортабельные части-панели, которые должны были изготавливаться на заводе, проходить контрольную сборку в отсеке и после этого отправляться на техническую позицию для сборки ракеты. Для окончательной сборки емкостей в монтажно-испытательном корпусе технической позиции предусматривалось сварочное отделение, где баки собирались из изготовленных и подогнанных на заводе предельно больших панелей, сваривались и проходили проверку на прочность и герметичность.
Эти конструктивно-технологические особенности ракеты требовали большого объема подготовки производства, большого количества крупногабаритного уникального нестандартизованного оборудования и оснащения, капитального строительства, а также решения сложных технологических проблем:
■ автоматической сварки алюминиевых сплавов толщиной от 6 до 16 мм;
■ обработки кромок крупногабаритных днищ и панелей баков под сварку;
■ обмера крупногабаритных баков с тарировкой;
■ контроля герметичности баков;
■ формовки заготовок оболочек баков путем обтяжки с растяжением листа;
■ взаимозаменяемости крупногабаритных отсеков при их стыковке;
■ изготовления и испытаний крупногабаритной арматуры (клапанов) и ряда других проблем.
Для сокращения цикла подготовки производства и решения технологических проблем ОКБ-1 параллельно с разработкой рабочей документации выдаются необходимые конструкторские и технологические данные по ракете Н1 для всех предприятий-смежников, создается бригада, в которую входят квалифицированные и опытные технологи А.А. Аксенов, Н.Г. Сидоров, Н.А. Заторяев, П.В. Лемешев, Б.П. Бабанов, Б.И. Колесников, О.М. Макаревич, А.Д. Шатский, В.П. Остолопов. К этой работе привлекаются технические службы завода "Прогресс", отраслевого технологического института НИТИ-40 и специалисты по сварочным работам Киевского института им. Патона и НИАТ МАП.
Главный конструктор С.П. Королев принял решение, одобренное вышестоящими органами, о создании ракеты Н1 в два этапа: первый — полное изготовление деталей, узлов, транспортабельных элементов агрегатов и проведение контрольных сборок на заводах-изготовителях; второй — сборка агрегатов и отсеков с проведением всех испытаний и общая сборка ракеты на технической позиции.
Для проведения работ по второму этапу на технической позиции потребовалось строительство специального монтажно-испытательного корпуса площадью около 11 000 м
2. В МИК намечалось провести следующие работы:
■ сборку и сварку топливных баков из элементов, выпущенных на заводах-изготовителях;
■ гидравлические и пневматические испытания с определением геометрических размеров и параметров баков;
■ сборку теплозащитного покрытия на баках блоков А, Б, В, монтажные работы и электропневматические испытания;
■ общую сборку ракеты и контрольные испытания по техническим условиям на ракету. Технологическая проработка и укрупненный технологический план работ позволили отраслевому проектному институту разработать технические задания на проектирование МИК и специального оборудования (около 80 единиц),
К этой работе привлекаются десятки предприятий, а заводу 88 поручается изготовление арматуры и рулевых машинок на все экспериментальные и три летные ракеты; изготовление экспериментальных блоков В (установка ЭУ-16) и проведение экспериментальных работ в НИИ-229 (г. Загорск).
Для выпуска узлов и агрегатов ракеты Н1 заводу требовались дополнительные производственные площади, новое оборудование и новые технологические решения.
Проводятся некоторые организационно-технические мероприятия:
■ организован участок изготовления крупногабаритной арматуры на территории цеха 7. Арматура (клапаны) ракеты Н1 по размерам, техническим условиям исполнения, особенно по посадочным уплотнительным местам, и эксплуатационным характеристикам была значительно сложнее и выше арматуры ракет, производимой заводом. Например, один из расходных клапанов 3011-0 имел массу более 50 кг, габариты 1000x600 мм. Специфика испытаний на соответствие эксплуатационным параметрам заключалась в проливке водой, а также компонентами топлива с большими расходами в различных средах, а испытаний на герметичность — проверкой гелием под давлением до 300 кгс/см
2;
■ создан отдел подготовки производства, в задачу которого входило составление комплексных графиков на экспериментальные и летные образцы, на изготовление отдельных установок и нестандартизованного оборудования;
■ организован участок вакуумных испытаний в цехе 5 для контроля герметичности узлов;
■ создан участок беспрессовой штамповки взрывом в цехе 14;
■ расширена действующая лаборатория сборки и испытания арматуры в цехе 3.
Два обстоятельства затрудняли изготовление в срок новой арматуры — количество клапанов и выполнение технических требований. По первому этапу комплектования всех экспериментальных установок для конструкторско-технологического изделия 1М на конструкторско-доводочные испытания и чистовые доводочные испытания требовалось 2930 клапанов 96 наименований, а на комплектование одной ракеты — 390 клапанов тех же наименований.
На территории цеха 7 организовывается лаборатория для сборки и испытания крупногабаритной арматуры. Эта лаборатория оснащается оборудованием, спроектированным и изготовленным силами завода. Такого большого количества арматуры завод не мог сделать в директивно установленные сроки. Решением вышестоящих организаций производится частичная разгрузка завода с последовательной передачей изготовления арматуры на завод "Прогресс", где строился для этого специальный корпус, и на завод 24 МАП (г. Куйбышев).
Большие трудности возникли с подготовкой производства и изготовлением первых комплектов рулевых машинок. Для комплектации ракеты Н1 требовалось 56 электрогидравлических рулевых машинок шести наименований. Конструкция этих приводов и их функционирование отличались от рулевых машинок других ракет.
Цех 3 помимо новых рулевых машинок продолжал изготовление рулевых машинок для ракет Р-9, РТ-1, РТ-2 и модификации ракеты Р-7. Кроме того, по указанию С.П. Королева в 1964 году в цехе 3 было изготовлено 60 комплектов рулевых машинок для проведения экспериментальной отработки двигателей на заводе 24 МАП (г. Куйбышев). Передать работу в другие цехи и разгрузить тем самым цех 3 было нецелесообразно, так как в цехе 3 были сосредоточены опытные специалисты и размещено специальное оборудование. Поэтому решили организовать новый специализированный цех 52.
Для стендовой холодной и огневой отработок третьей ступени (блок В) на заводе была изготовлена установка ЭУ-16. Планировалось сделать четыре таких установки для проведения испытаний в течение ряда лет. Работа для коллектива завода была довольно сложной, а сроки изготовления — сжатые. Тщательная проработка технологических процессов определила необходимую оснастку, насчитывающую около 750 единиц.
В июне 1965 года установка в разобранном виде доставляется с завода в НИИ-229 (г. Загорск), где в монтажном корпусе проводились сборочно-монтажные работы. Топливные баки изготавливал завод "Прогресс", окончательная сборка и сварка этих баков проводилась также в монтажном корпусе НИИ-229. Для отработки систем разделения и сброса панелей отсеков на научно-испытательном полигоне в г. Загорске (директор B.C. Лыжков) проводилась сборка крупногабаритных отсеков блоков Б и В установок ЭУ-2, ЭУ-3 и других. Главная трудность заключалась в том, чтобы обеспечить транспортировку установок после их сборки к месту разделения и сброса.
Работы по теме Н1 на заводе находились под постоянным контролем С.П. Королева. В помощь конструкторам отдела главного технолога завода было направлено 46 инженеров из отделов КБ, несмотря на большой объем работы в конструкторских отделах.
Продолжалось изготовление экспериментальных установок ЭУ-16, ЭУ-15 и других узлов и агрегатов для проведения испытаний. Не прекращались огневые, конструкторско-доводочные и другие испытания с агрегатами и узлами изделия. Построенный монтажно-испытательный корпус ракеты-носителя на технической позиции необходимо было оснастить уникальным технологическим оборудованием, крупногабаритной оснасткой, другими видами технологического оборудования, необходимого для обеспечения сварочных, сборочных и испытательных работ.
Для координации и контроля за ходом изготовления этого оборудования и оснащения на смежных предприятиях, определенных постановлениями Правительства и договорными отношениями, при ОГТ была организована группа технологов как филиал 2 под руководством заместителя главного технолога В.П. Долбилова.
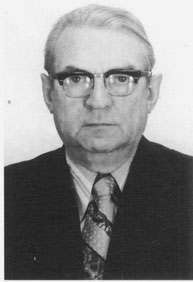
В.М. Ключарев |
Технологам этой группы совместно со специалистами завода "Прогресс" приходилось очень часто бывать на заводах, выпускающих оборудование и оснастку. В случае каких-либо затруднений, связанных со сроками изготовления, или отказа от изготовления, им приходилось для решения этих вопросов обращаться в соответствующие министерства, Госплан СССР, к секретарям обкомов, парткомов предприятий и т.д. Особенную настойчивость и активность в решении этих вопросов проявлял В.В. Чистяков.
Одновременно с изготовлением тяжелой ракеты-носителя Н1 началась подготовка производства для изготовления полезной нагрузки — головного блока. Полезная нагрузка ракеты Н1 представляла собой головной блок длиной 43 м, максимальным диаметром 6 м и массой более 90 т. Весь этот комплекс (ракета-носитель Н1 — головной блок) получил название Н1-ЛЗ (11А52).
Во второй половине 1966 года на предприятии проводится структурная перестройка, в том числе и завода.
Завод стал называться Заводом экспериментального
машиностроения (ЗЭМ). Директором назначается В.М. Ключарев, главным инженером — В.Д. Вачнадзе, главным технологом — В.Е. Гальперин.
Производства на 1-й и 2-й территориях были упразднены и разделены на ряд производств с учетом уже имеющихся специализированных производств. Заместителем директора по производству назначается И.Б. Хазанов, начальником арматурно-двигательного производства — А. А. Борисенко, начальником приборного производства — Г.Б. Николаев. Организовываются новые производства:
■ агрегатное производство (начальник П.И. Кежаев) — цехи 408, 414, 440, 445;
■ механозаготовительное производство (начальник Л.Л. Маневич) — цехи 411, 412, 417, 406, 443, 478;
■ сборочное производство (начальник А.П. Собко) — цехи 413, 415, 439, 444;
■ инструментальное производство (начальник В.Г. Пеев) — цехи 427, 428, 446.
Заместителем главного инженера по новой технике и реконструкции становится В.М. Рожков, первым заместителем главного инженера — М.С. Козлов.
После структурной перестройки производств все подразделения завода получили новые обозначения, например, цех 8 получил обозначение 408; цех 40 — 440 и т.д.
С 1966 года на завод стала поступать рабочая документация на головной блок и входящие в него составные части: блок Д, переходник, лунный орбитальный корабль 11Ф93 и лунный корабль 11Ф94.
Разгонные ракетные блоки Г и Д, переходник и корабли 11Ф93 и 11Ф94 собирались последовательно в горизонтальном положении в единую сборку, к которой стыковалось переходное кольцо от обтекателя, и весь этот "комплекс" укладывался в нижнюю половину обтекателя и закрывался его верхней половиной.
Из-за конструктивно-технологических особенностей головного блока и больших габаритов, не позволяющих транспортировать собранный головной блок на технический комплекс, принимается технология изготовления, аналогичная технологии изготовления ракеты Н1, те. создание транспортабельных агрегатов, блоков и элементов на заводах-изготовителях и окончательная сборка на ТК.
Работы по созданию головного блока и составляющих его изделий распределялись следующим образом:
■ ЗЭМ — изготовление кораблей 11Ф93, 11Ф94, блоков Д, верхнего переходника, а также проведение экспериментальных работ; работы на ТП по досборке кораблей 11Ф93, 11Ф94, блока Д, по сборке комплекса и головного блока в целом, проведение пневмо— и электроиспытаний, контроль геометрических параметров комплекса и головного блока в целом, стыковка головного блока к ракете-носителю Н1 в МИК;
■ завод им. Хруничева (директор завода М.И. Рыжих) — изготовление головного обтекателя;
■ завод "Прогресс" (директор завода А.Я. Линьков) — изготовление блока Г.
Если ЗЭМ мог справиться с объемом подготовки производства по изготовлению кораблей 11Ф93, 11Ф94, блока Д, верхнего переходника непосредственно на заводе, то для подготовки производства на ТП у завода не было ни технических возможностей по изготовлению крупногабаритного оборудования, ни необходимых производственных мощностей.
Для организации работ на ТП нужно было спроектировать и изготовить стенды для досборки кораблей 11Ф93 и 11Ф94, стенды обслуживания блоков Д и Г, монтажно-стыковочные тележки (12 наименований), стапель сборки головного блока со средствами обслуживания, две тележки с кольцами диаметром 6 м для обеспечения вращения на 360° комплекса и головного блока при контроле геометрических параметров и т.д. Много работ по проектированию и изготовлению оснастки для ТП завод выполнял своими силами.
Для выполнения работ с изделиями на ТП привлекаются сторонние организации и предприятия.
Учитывая, что лунный орбитальный корабль 11Ф93 создавался на базе корабля 7К-ОК и базовые отсеки корабля были в основном аналогичны отсекам этого корабля, вновь создаваемая большая часть оснастки могла быть использована для корабля 11Ф93. Изготовление отсеков и агрегатов проводилось в тех же цехах. Сборка отсеков и агрегатов корабля 11Ф93 проводилась в цехе 444 (начальник цеха Г.М. Марков). Блок И корабля 11Ф93 завод получал по кооперации, а общую (главную) сборку проводил цех 439А на ТП, а затем — вновь созданный цех 441 (начальник цеха В.И. Кожухов).
Агрегаты энергетического отсека и блока двигателей ориентации комплекса были новыми, подготовка их производства велась в полном объеме.
Изготовление системы энергопитания было поручено цехам арматурно-двигательного производства. Изготовление узлов, сборка и испытания СЭП в ЭО проводились в цехе 405, испытания и сборка арматуры — в цехах 403, 407.
Для отработки СЭП создается экспериментальная база на 3-м производстве.
Изготавливались многочисленные экспериментальные установки. В связи с неудачными испытаниями ракеты-носителя Н1 изготовление штатных кораблей 11Ф93 не состоялось, и работы были прекращены.
Аналогов лунного корабля не было, и поэтому подготовку производства ЛК пришлось выполнять практически с "нуля". Агрегаты ЛК изготавливались в основном в цехе 440. Сборка проходила в цехе 439.
Изготовление корпусов лунного корабля особых трудностей не представляло. Из новых технологий было освоено изготовление вафельного днища с механической обработкой вафельной зоны на станке с числовым программным управлением и последующей штамповкой днища, а также изготовление сотовых поглотителей энергии для посадочных устройств.
Было изготовлено много компонентов материальной части для проведения различного вида испытаний — статических, динамических, тепловых и т.д. Особое внимание уделялось копровым испытаниям лунных посадочных устройств.
Для проведения сборочно-монтажных работ на технической позиции потребовались новые производственные площади, так как в МИК, где собиралась ракета Н1, производственных помещений и площадей для размещения головного блока и его составляющих не хватало. Было принято решение использовать монтажно-испытательный корпус космических объектов (135Р-2Б).
В МИК КО проводились следующие работы:
■ сборка корабля ЛОК (11Ф93) из транспортабельных агрегатов;
■ сборка головного блока;
■ проведение работ с блоками Г и Д после их транспортировки;
■ досборка корабля ЛОК (11Ф94);
■ сборка обтекателя 11А52;
■ сборка комплекса 11А52;
■ сборка и контроль геометрических параметров комплекса и головного блока;
■ проведение пневмо— и электроиспытаний.
Подготовка производства по изготовлению лунного орбитального корабля (11Ф93), ЛК (11Ф94), блоков Д и Г и подготовка к сборке головного блока на ТП практически осуществлялись в одно и то же время, что вызывало дополнительные трудности в организации работ. Объем работ по подготовке производства и сборке головного блока и входящих в него изделий на ТП был достаточно большим. Помимо этого, необходимо было организовать и соответствующие службы для обеспечения всех работ на технической позиции.
Для этого и в целях организации производства по сборке макетно-технологического головного блока 1М1 изделия 11А52 в МИК КО (объект 135Р-2Б) и выполнения утвержденного графика по сборке головного блока 1М1 приказом по предприятию от 12 октября 1967 года на объекте 135Р-2Б был организован филиал сборочного производства в составе:
■ сборочного цеха 439А;
■ цеха комплектации 425А;
■ техотдела;
■ службы подготовки производства и эксплуатации;
■ секции ОТК завода.
Общее руководство проведением работ по блоку 1М1 было возложено на исполняющего обязанности главного инженера филиала 2 ЦКБЭМ Ю.И. Лыгина, руководство филиалом производства — на начальника сборочного производства А.П. Собко, цехом 439А — на начальника цеха 439 В.И. Мытарева и на исполняющего обязанности начальника техотдела А.Д. Шатского, цехом 425А — на В.М. Болотина. Комплектование кадрами осуществлялось из сотрудников этих же подразделений, а техотдела — дополнительно из числа технологов филиала 2 ЦКБЭМ на ТП. На главного механика филиала 2 на ТП И.М. Вишнякова были возложены обязанности обеспечивать работы технологической оснасткой и осуществлять руководство монтажом технологического оборудования.
В процессе сборки кораблей 11Ф93, 11Ф94, работ с блоками Г и Д, другими агрегатами, а также сборки комплекса, головного блока необходимо было провести проверку всего технологического оборудования и оснастки и их отработку, а также отладить технологический процесс сборки головного блока.
Основные трудности при подготовке производства и проведении сборочных и контрольных работ на ТП возникали из-за больших габаритов головного блока, большого количества изделий, входящих в него, и необходимости проведения сборки и контроля геометрических параметров в горизонтальном положении головного блока.
Опыта работ по сборке и контролю геометрических параметров изделий таких габаритов и такой конструкции в нашей промышленности и в мировой практике не было. Для этих целей пришлось создавать специальное оборудование, позволяющее вращать вокруг горизонтальной оси как комплекс, так и сам головной блок.
В процессе проведения сборочных работ с изделием 1М1 было отработано почти все основное оборудование, а также и оснастка. Объем работ по сборке изделия 1М1 показал, что для сборки штатного изделия требовалась более фундаментальная подготовка технологической документации. С этой целью на ТК образовывается технологический отдел 459 (начальник Н.А. Ашихменов), цех 439А преобразован в цех 441 (начальник В.И. Кожухов). Руководителем всех этих служб и ответственным за все подразделения завода на ТП назначается заместитель главного инженера завода Ю.И. Лыгин, заместителем начальника производства на ТП становится Г.В. Вишняков. Все эти организационные мероприятия проводились в 1968-1969 гг. Сборка головного блока Л1Э с упрощенными кораблями для изделия Н1 № 3Л в 1968 году была осуществлена без особых затруднений, за исключением контроля геометрических параметров комплекса и головного блока в целом.
Проведение первого же контроля геометрических параметров изделия выявило значительную погрешность измерений. Анализ показал, что на увеличение погрешности сильно влияет перепад температур воздуха по высоте МИК КО (до 5-10°С), вызывающий деформацию изделия. Была проведена реконструкция МИК КО (построен тамбур у выездных ворот МИК КО) и улучшена система отопления корпуса. Кроме того, была разработана специальная методика контроля геометрических параметров. Впоследствии методики сборки головного блока и контроля геометрических параметров были защищены авторскими свидетельствами, а на методику контроля геометрических параметров был выпущен отраслевой стандарт.
В решении этих задач активное участие принимали Б.И. Колесников, В.Е. Гальперин, Н.А. Ашихменов, А.Д. Шатский, Б.Д. Хрусталев, Г.В. Вишняков, В.В. Чистяков, Ю.И. Лыгин, В.И. Беляков и др.
В 1972 году принимается решение о приостановке изготовления кораблей 11Ф93 и 11Ф94, а в 1974 году — о приостановке работ по Н1-Л3, а еще через два года — о разборке собранных ракет и консервации оборудования. Технологический отдел 459 реорганизуется в техбюро цеха 425, а цех 441 объединяется с цехом 425 в единый экспериментально-сборочный цех в составе сборочного производства с присвоением ему номера 425. Начальником цеха 425 назначается В.И. Кожухов. Остальные службы расформировываются.
Изготовление блоков Д и ДМ
В 1965-1967 гг. на завод стала поступать документация на разгонные ракетно-космические блоки Д изделий 11С824 и 11А52.
Принципиальная разница этих блоков состояла в различии систем управления блоками и наличии переходника с большим диаметром у блока Д изделия 11С824 для обеспечения стыковки с ракетой-носителем 8К82К ("Протон").
Изготовление деталей, узлов и агрегатов для блока Д осуществлялось в цехах 1-го производства, сборка проводилась в цехе 439.
Предусматривалось также изготовление двигательной установки этого блока.
Для экспериментальных работ было изготовлено 188 двигателей, на которых было проведено 462 испытания, в том числе и огневые. В результате был выбран основной вариант двигателя. Изготовление и отработку двигателя проводил цех 405 совместно с конструкторами КБ.
Одним из сложных агрегатов в двигателе 11Д58 был блок подачи окислителя. При его проектировании намечались два пути создания тракта для подачи к ДУ переохлажденного кислорода (корпус, трубопроводы): первый — блок подачи из металла, требующий специальной изоляции и имеющий значительные тепловые потери; и второй, абсолютно новый путь, — из неметалла, никем и никогда не применявшегося в двигателестроении. Сложными в отработке были также неохлаждаемый насадок двигателя, большое количество паяных соединений и многое другое.
Молодые технологи ОГТ и руководители В.М. Василевский, В.Е. Гальперин, В.И. Житомирский вместе с конструкторами ОКБ М.В. Мельниковым, Б.А. Соколовым, Ю.Ф. Гавриковым и только что назначенными начальником арматурно-двигательного производства А.А. Борисенко и начальником цеха 405 Б.М. Бочаровым в кратчайшие сроки создали, изготовили и отработали эти сложнейшие узлы, которые до настоящего времени считаются лучшими в существующих ЖРД.
Подготовка производства к изготовлению блока Д была трудной: требовались крупногабаритные штампы для изготовления элементов баков и оборудования для их сварки, стапельная оснастка для сборки-клепки переходников, сварки ферм, стендов главной сборки и т.д.
Трудности подготовки усугубились жесткими требованиями к точности изготовления, отклонениями от теоретической линии обводов баков, высокими требованиями к чистоте внутренних полостей баков и пневмогидромагистралей и т.д. Всего для изготовления блоков всех модификаций понадобилось свыше 8700 наименований оснастки, в том числе 3300 наименований приспособлений (с учетом крупногабаритных).
При проектировании изделий таких габаритов, как блок Д, особое внимание обращалось на уменьшение массы изделия за счет применения высокопрочных алюминиевых и титановых сплавов и высокопрочных сталей. Так, был использован высокопрочный сплав типа АК8 для крупногабаритных шпангоутов, изготавливаемых вначале из кованых колец, а затем из раскатных колец в закаленном и искусственно состаренном состоянии.
Основным дефектом окончательно изготовленных шпангоутов из этих колец была деформация шпангоутов — эллипсность и неплоскостность после карусельной и фрезерной обработок. Его удалось с трудом устранить только после механической обработки с равномерным съемом металла с каждой стороны и межоперационного "вылеживания" в течение длительного времени для релаксации напряжений, вызывающих деформацию.
Отработкой и внедрением этой технологии занималась группа технологов в составе А.И. Кузнецова, Л.И. Шихолина, В.П. Николаева, Н.С. Ромашова.
Сложным было и изготовление шаровых баллонов из титанового сплава ВТ6, работающих погруженными в жидкий кислород. В конструкции использована высокая прочность сплава и эффект ее повышения в результате охлаждения до -183°С.
За короткое время в цехе 408 были установлены вакуумные камеры для сварки, в цехе 438 — вакуумные печи для отжига.
Непростым и трудоемким было изготовление элементов сферических баков окислителя и торовых днищ для баков горючего и приборных отсеков. Так, цельнотянутые тонкостенные алюминиевые полусферические днища без сварного шва могли быть изготовлены максимальным диаметром только около 2000 мм из-за ширины листа 3000 мм. Для изготовления же элементов бака окислителя диаметром 2660 мм требовались только сварные заготовки. Ранее сферический пояс изготавливался из четырех частей, с последующей подгонкой, правкой и т.д. Это был длительный и трудоемкий процесс.
Чтобы исключить его, была предложена штамповка взрывом целого сферического пояса из конической заготовки. Это сократило трудозатраты на 177 ч, снизило расход металла на 100 кг, сократило производственный цикл на 8 смен и долю медницких работ — на 70%. Для получения точных обводов и размеров торовых днищ (для баков горючего и приборного отсека) применялась технология штамповки под прессом с последующей калибровкой взрывом. Однако калибровка взрывом крупногабаритных торовых днищ — процесс длительный и трудоемкий. Он требует промежуточного и окончательного отжига с заневоливанием в кольце по наружному диаметру, а при транспортировании на участок штамповки взрывом были возможны повреждения наружного обвода и т.д.
Чтобы устранить эти недостатки, было предложено калибровку торовых днищ производить на оправке (приспособлении) специальной конструкции под прессом мощностью 1000 тс в нагретом состоянии, что сократило производственный цикл на 52 ч, сохранило качество и точность изготовления и дало возможность производить работы на едином производственном участке.
Таких примеров решения сложных технологических задач было множество.
Внедрялись новые методы формообразования деталей из листовых материалов, например магнитно-импульсная штамповка, основанная на преобразовании электрической энергии в энергию магнитно-импульсного поля, совершающего работу по деформации заготовки. Активное участие в решении этих и многих других задач принимали П.В. Лемешев, Б.И. Васильев, В.В. Кононов, В.И. Самосадный, Т.А. Голиусов, К.Б. Давыдова, П.Г. Егоров, А.Г. Петров и другие.
Изготовление основных агрегатов и отсеков блока Д происходило в цехах 408 и 440.
В цехе 408 изготавливались шар-баллоны и емкости высокого давления из высокопрочных сталей и титановых сплавов, крупногабаритные рамы и фермы из алюминиевых, титановых сплавов с использованием неметаллических стержней.
При изготовлении этих изделий внедрялось уникальное оборудование:
■ вакуумные камеры для автоматической сварки титановых шар-баллонов в контролируемой среде;
■ стенд для холодных испытаний шар-баллонов;
■ измерительные программные устройства с записью результатов;
■ автоматические сварочные головки для сварки неповоротных стыков труб в рамах и фермах и т.д.
Непосредственное участие во внедрении этих технологий и оборудования принимали Д.Д. Мирошин, Ю.Е. Гульянц, И.А. Комоедов, Г.И. Панина, А.В. Панин, С.А. Арефьев, Г.П. Галкин и другие.
В цехе 440 изготавливались баки горючего и окислителя, клепаные отсеки и герметичные приборные отсеки в виде торовых емкостей (разъемных полуторов с механическим соединением между собой с резиновым уплотнением).
Много сил в освоении технологии изготовления баков приложили Н.А. Заторяев, Н.А. Каменский, Н.К. Котов, A.M. Манегин, Н.А. Терехов, П.В. Домокеев, И.Е. Кремнев, П.Г. Чайкин, В.П. Тарасов, С.А. Колобов.
Большую помощь оказывали работники ОГТ и ОГС В.Г. Ерофеев, В.П. Горин, А.И. Ломакин, Ю.Л. Яровинский, Н.М. Панферов и другие.
Главная сборка блоков Д производилась в боковом пролете цеха 439. Из-за конструктивно-технологических особенностей блока Д, высоких требований к точности установки двигателей, удобства обслуживания и других требований была выбрана вертикальная схема сборки.
Размещение стенда сборки модульной части блока Д в боковом пролете цеха создавало дополнительные трудности. Высота до подкрановых путей в боковом пролете (12 м) не позволяла производить сборку в стенде, и потребовалось заглубить стенд почти на 2 м.
Для выполнения заданной программы сборки (12-18 блоков Д в год при цикле сборочных работ около 60 дней) было изготовлено два стенда. Стенды были установлены стационарно, на фундаменте. Требования к точности и ее стабильности были достаточно высокими, так, например, стенд должен был обеспечить установку модуля базовым шпангоутом с наклоном оси модуля не более 8'.
В стенде проводились стыковка двигателя, выверка нулевого положения оси двигателя относительно оси блока, совмещение механического и электрического нулей рулевых машинок двигателя, определение усилий при прокачке камеры сгорания двигателя, контроль положения посадочных плоскостей под установку приборов и другие контрольные работы. Здесь же проводились монтаж арматуры, трубопроводов со сваркой стыков, испытания на герметичность и т.д.
В 1985 году, после перебазирования цеха 439 (начальник В.И. Мытарев) в корпус 6, стенды в напольном исполнении были окончательно установлены. Сборка блоков в них ведется по настоящее время.
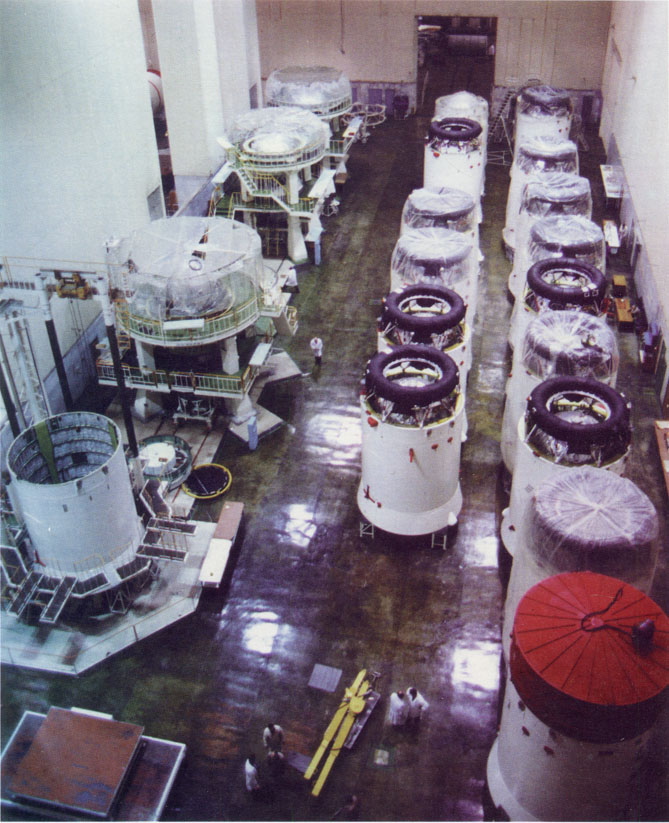 | | Пролет цеха 439. Участок главной сборки
блоков Д
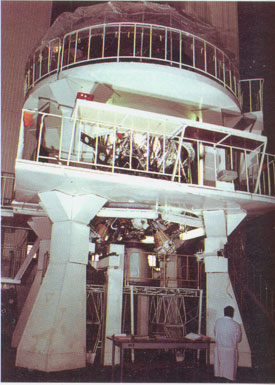
Стенд главной сборки разгонных блоков ДМ в
цехе 439 |
Освоение технологии сборочно-испытательных работ повлекло решение сложных технических вопросов. Так, испытания на герметичность бака окислителя с установленной арматурой со стеклопластиковыми корпусами, с фланцевыми соединениями и уплотнительными прокладками проводились в условиях, максимально приближенных к условиям эксплуатации бака окислителя, т.е. при низкой температуре и глубоком вакууме, Поэтому на 2-м производстве была оборудована барокамера для установки бака окислителя со сложными системами заправки (слива) жидким азотом при температуре -196°С, системой наддува бака окислителя газообразным гелием, системой контроля негерметичности (метод "захолаживания"). При проверках бака окислителя с арматурой в "захоложенном" состоянии иногда обнаруживалась негерметичность во фланцевых соединениях и стеклопластиковых корпусах арматуры. В обычных условиях контроля этот дефект не обнаруживался.
Начиная с первых блоков Д, контроль герметичности методом обмыливания заменили на более точный и объективный метод "щупа" с помощью гелиевых течеискателей, контролирующих натекание в местную разъемную вакуумную камеру каждого
контролируемого стыка.
Эти новые методы контроля герметичности значительно повысили надежность испытаний, позволили выявить некачественную сборку, сварку и дефекты по металлу. Блок Д отрабатывался на специально изготовленных отсеках для статических и динамических испытаний, блоках для стендовых огневых испытаний, блоках отработки заправки топливом, газами, для отработки экранно-вакуумной теплоизоляции и системы наддува оболочки воздухом.
Для повышения элементов надежности пневмогидросистем большинство разъемных соединений трубопроводов друг с другом, с агрегатами и клапанами (так называемые монтажные стыки трубопроводов) были заменены на сварные, неразъемные стыки, после этого проводился рентгеноконтроль сварных стыков, что значительно повышало надежность изделия по герметичности.
Были изготовлены сварочные машинки с поворотными головками разных типоразмеров, проведено переэталонирование трубопроводов, введены специальные наконечники и т.д.
Для обеспечения программы выпуска блоков принимается решение об организации поточно-позиционной сборки модуля 11С85 и его основных агрегатов. Разрабатываются технологическая документация (техпроцессы, паспорта, комплектовочные карты), положения по организации внутрицехового планирования на основе циклосетевых графиков в условиях поточно-позиционной сборки в цехе 439, изготавливается дополнительная оснастка и т.д.
При переходе к этому методу сборки учитывался метод поточно-позиционной сборки, внедренный на заводе при сборке кораблей 7К-Т (11Ф615А8).
Дальнейшая модификация блоков Л (11С861, 11С861-0, 17С40, 11С824Ф) была обусловлена необходимостью их унификации на базе единого модуля 11С861, который включал баки окислителя и горючего, двигатель 11Д58М, переходник и фермы для связей баков двигателя.
Многие работники цеха 439 внесли значительный вклад в дело развития технологии изготовления блока Д. Среди них В.И. Мытарев, Р.М. Шишонков, А.И. Додонов, М.А. Горбачев, М.И. Ломакин, Н.И. Антонов, А.И. Дубасов, М.А. Лазарев, В.Н. Юдин, Н.M. Стуковнин, М.С. Волков, A.M. Соловьев, Б.П. Патрикеев, Б.И. Колесников и многие другие работники цеха и завода.
далее
назад